When it comes to forklift repair, many business owners and operators consider DIY fixes to save time and money. However, this can often lead to costly mistakes that could compromise both safety and efficiency. Forklifts are complex machines, and repairing them without proper knowledge or tools can result in severe consequences, including safety hazards and extended downtime.
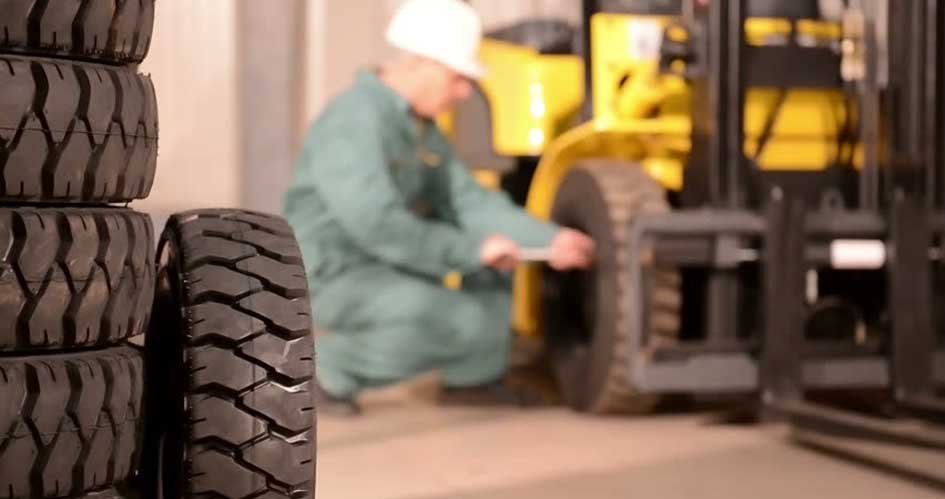
In a busy work environment, these issues can disrupt operations, put workers at risk, and ultimately lead to significant financial losses. Understanding the common DIY forklift repair mistakes and knowing when to call a professional is crucial for maintaining a safe and efficient operation. In this article, we’ll discuss key mistakes to avoid and provide tips on how to ensure your forklift repairs are done right the first time.
Key Mistakes in DIY Forklift Repairs
Forklift repairs can seem straightforward, but even a small error can lead to serious consequences. Below are some of the most common mistakes people make when attempting DIY forklift repairs.
1. Ignoring the Forklift’s Maintenance Manual
Forklift maintenance manuals are essential for proper repair and maintenance procedures. These manuals offer valuable information on how to maintain your specific forklift model and troubleshoot common issues. Ignoring this guide can result in missed steps, unaddressed blind spots, and improper fixes that may worsen the problem. Whether it’s a modern forklift or a gas-powered model, sticking to the manufacturer’s instructions is key for ensuring long-term functionality and avoiding unnecessary repairs. Following the manual helps prevent potential hazards and ensures that all safety features are correctly implemented.
2. Using Incorrect or Low-Quality Replacement Parts
Using low-quality or incorrect replacement parts is one of the most significant mistakes in forklift repairs. Inferior parts, such as faulty tires or substandard hydraulic components, can drastically impact forklift operation. Not only do they reduce the performance of your forklift, but they also lead to more frequent repairs, increased downtime, and even serious accidents in the work area. It’s essential to use high-quality, OEM (original equipment manufacturer) parts that are specifically designed for your forklift. Whether you’re repairing a diesel engine or electric forklift, sourcing parts from reliable suppliers is non-negotiable.
3. Overlooking Safety Procedures and Precautions
Safety should always be a priority when repairing forklifts. Overlooking safety procedures, such as failing to wear seatbelts, ignoring light signals, or neglecting to maintain a safe workspace, can lead to severe accidents or injuries. Common oversights can include working in an unsafe environment or overlooking key safety signs.
Qualified technicians, on the other hand, are trained to follow safety protocols strictly, which minimizes the risk of injury to forklift operators and pedestrians. When performing repairs, make sure your work area is clear of obstructions and that all safety features are functioning properly.
4. Failing to Properly Diagnose the Problem
Jumping into repairs without thoroughly diagnosing the issue is a risky mistake. Misdiagnosing forklift problems can lead to unnecessary repairs, wasted time, and additional costs. It’s essential to fully understand the issue before attempting any repairs. For instance, problems with forklift engines (whether gasoline or diesel) may be mistaken for issues with the hydraulic systems.
The complexity of modern forklifts or electric models requires a trained eye to accurately pinpoint the problem. Taking time to properly diagnose the issue before starting repairs can save time, reduce costs, and ensure that the right repairs are made to address the root cause.
5. Skipping Regular Maintenance Checks
Skipping regular maintenance checks is one of the most common mistakes forklift operators make. Ignoring routine inspections of vital systems, such as tires, engines (gasoline/diesel), ignition, and hydraulic components, can lead to severe breakdowns. Issues left unchecked can escalate quickly, resulting in major failures that cause costly downtime.
Regular maintenance ensures that all components are functioning optimally and helps identify potential problems before they become serious. By sticking to a proper service plan and performing regular checks, forklift owners can avoid unexpected repairs and maintain safe, efficient operations.
6. Undertaking Complex Repairs Without Proper Tools or Experience
When attempting complex forklift repairs, such as fixing heavy loads or dealing with intricate systems like forks or hydraulic mechanisms, using improper tools or lacking sufficient experience can cause more harm than good. Forklifts are sophisticated machines, and without the correct tools or knowledge, there is a high risk of disrepair, leading to safety hazards, more downtime, or even injury. It’s always a good idea to call a qualified technician for these types of repairs. Trained professionals are equipped with the right tools and expertise to handle issues efficiently and ensure your forklift is safe to use.
7. Neglecting the Hydraulic System
The hydraulic system is one of the most critical components of a forklift. Neglecting it can lead to serious operational failures and costly downtime. Faulty hydraulic systems can impact lifting, steering, and other essential forklift functions. Since hydraulic systems rely on fluid pressure to operate efficiently, any issues with leaks, fluid levels, or pressure can cause complete breakdowns.
Regular checks and servicing of the hydraulic system are essential to ensure the forklift continues to operate safely and efficiently. Neglecting this system not only compromises forklift performance but also puts operators and pedestrians at risk.
How to Avoid Common DIY Forklift Repair Mistakes?
To avoid costly mistakes and ensure forklift safety and performance, it’s important for business owners and forklift operators to adopt a proactive approach to maintenance. Here are a few actionable tips to help improve your forklift repair strategy.
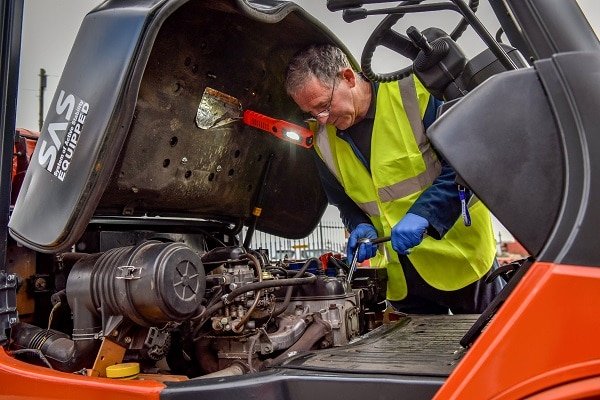
Understanding the Importance of the Maintenance Manual
Reading and understanding the forklift maintenance manual is crucial for both operators and service providers. These manuals provide essential instructions on how to maintain and repair your forklift safely and effectively. By following the manual’s guidelines, operators can prevent unnecessary downtime and reduce the risk of collisions and accidents in the workplace. It’s always a good idea to keep the manual accessible and review it regularly to stay updated on proper procedures. Following these guidelines ensures that the forklift operates as designed, reducing work-related hazards and improving overall efficiency.
Choosing the Right Parts and Tools for the Job
Selecting the right replacement parts and tools is essential for the reliable operation of your forklift. Always opt for OEM (original equipment manufacturer) parts that are specifically designed for your forklift model, whether it’s an electric forklift or a gas-powered (gasoline or diesel) unit. Using high-quality parts ensures that your forklift operates smoothly and minimizes the risk of mechanical failure.
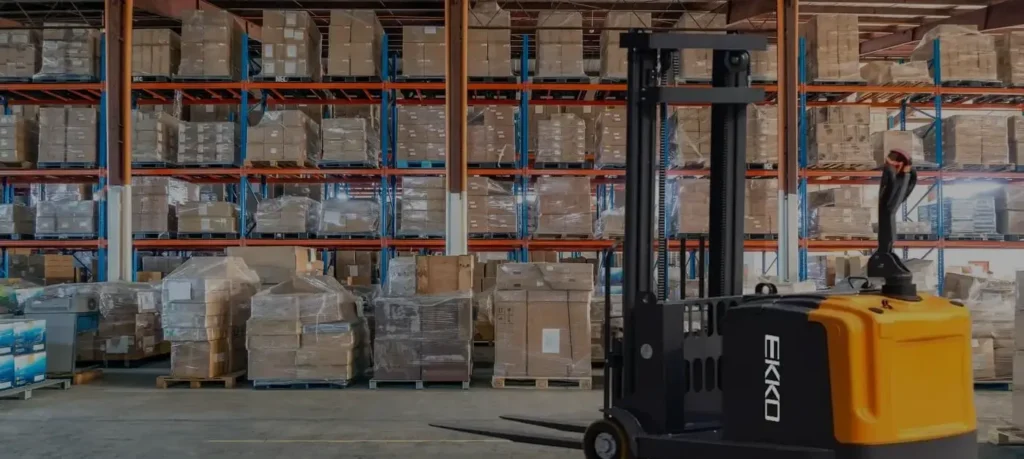
Additionally, make sure to have the proper tools for complex repairs—using the right equipment reduces the likelihood of damage during the repair process and ensures that everything is put back together correctly.
Emphasizing Safety First in All Repair Tasks
Safety should always be a top priority when performing any forklift repairs. Operators must wear the appropriate safety gear, such as seatbelts and helmets, and follow all safety signs in the workspace. Ensuring that the work area is clear of obstructions and well-lit can significantly reduce the risk of accidents.
Proper training also plays a critical role in reducing risks—when operators understand the proper handling of forklifts and are trained in safety protocols, the risk of injury to both themselves and pedestrians is minimized. Always adhere to safety procedures to ensure that repairs don’t lead to more problems.
Conclusion
Forklift repairs are essential to keeping your operations running smoothly, but DIY fixes can lead to serious issues if not done correctly. Hiring a qualified technician ensures that your forklift remains in top working condition, reducing downtime and preventing accidents. By avoiding common DIY mistakes, such as neglecting maintenance, using low-quality parts, and overlooking safety protocols, you can improve your fleet’s performance and safety.
At Upright Forklift Repair, we specialize in forklift repair and maintenance services in Houston and Humble. Our experienced technicians are equipped to handle all your forklift needs, so don’t hesitate to contact us for professional and reliable service.
What are the risks of DIY forklift repairs?
While DIY forklift repairs may seem like a cost-effective option, they carry significant risks. Improper repairs can lead to major safety hazards, including collisions, operational failures, and increased downtime. If not done correctly, DIY repairs can cause costly mistakes, such as using the wrong parts or damaging key forklift systems like the hydraulic system or tires.
These risks can ultimately result in serious accidents and injuries, as well as disruptions in forklift operations, which affect business productivity. To avoid these issues, it’s always best to hire a professional forklift repair service. Contact Upright Forklift Repair for expert service in Houston and Humble to ensure your forklifts are safe, functional, and running at their best.