Maintaining a regular service schedule for your forklifts is essential to ensuring safety, efficiency, and cost-saving in your operations. Forklifts are vital assets in warehouses, construction sites, and various industrial settings, but their daily use can lead to wear and tear. Understanding how often you should service your forklift is key to preventing breakdowns and keeping operational costs low. Forklift maintenance not only keeps your equipment running smoothly but also enhances productivity and reduces downtime.
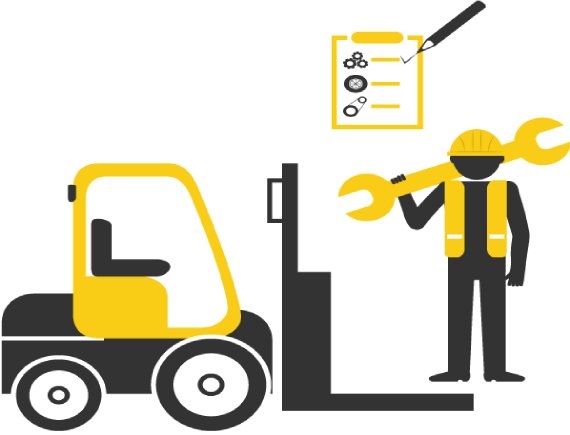
For most businesses, following a consistent forklift maintenance schedule offers a proactive approach to address potential issues before they escalate into costly repairs. Regular forklift maintenance, tailored to the type of forklift and its usage, helps improve overall safety by minimizing the risk of malfunctions that could endanger operators and nearby employees. With the right preventative maintenance plan in place, companies can avoid frequent breakdowns and ensure their forklifts operate at peak performance, contributing to long-term cost efficiency and equipment longevity.
Why Regular Forklift Maintenance Matters?
Regular forklift maintenance is crucial for any business that relies on lift trucks to keep operations running efficiently. The benefits of maintaining a regular service schedule for your forklifts go beyond immediate functionality—routine maintenance can significantly reduce repair costs over time. By addressing wear and tear proactively, companies can catch minor issues before they turn into more expensive repairs, keeping maintenance costs manageable.
Frequent maintenance also improves safety by ensuring forklifts operate reliably and safely, reducing the chance of accidents. This attention to detail contributes to a safer environment for operators and other team members working around lift trucks. Furthermore, a well-maintained forklift typically has a longer operational life, providing a higher return on investment and minimizing the need for premature equipment replacement.
Benefits of a Forklift Maintenance Schedule
A structured forklift maintenance schedule is crucial to ensure forklifts operate efficiently and stay in service longer. By establishing maintenance intervals based on manufacturer recommendations and operational demands, companies can proactively manage potential issues. This approach, known as preventative maintenance, allows for early detection of wear and tear, keeping forklifts in optimal condition.
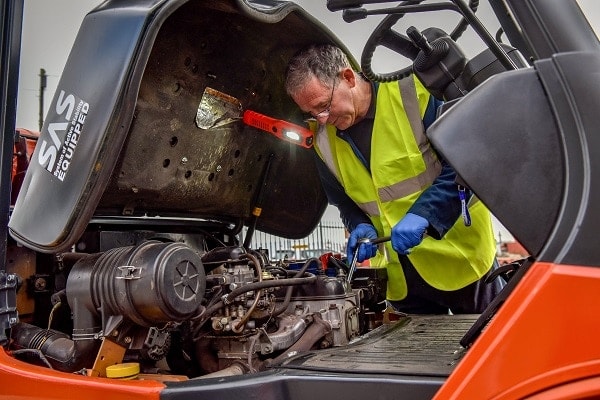
Scheduled maintenance not only helps prevent unexpected breakdowns but also reduces downtime, as well-maintained forklifts are far less likely to experience sudden mechanical issues. Additionally, a consistent schedule minimizes costly emergency repairs and extends the life of each forklift, ultimately saving on long-term expenses. By adhering to a dedicated maintenance plan, companies ensure that their lift trucks stay safe, efficient, and cost-effective.
Key Factors That Determine Forklift Maintenance Frequency
The frequency of forklift maintenance visits depends on multiple factors, such as hours of use, type of forklift, and operating environment. Establishing an optimal service interval based on these factors is essential for both performance and longevity.
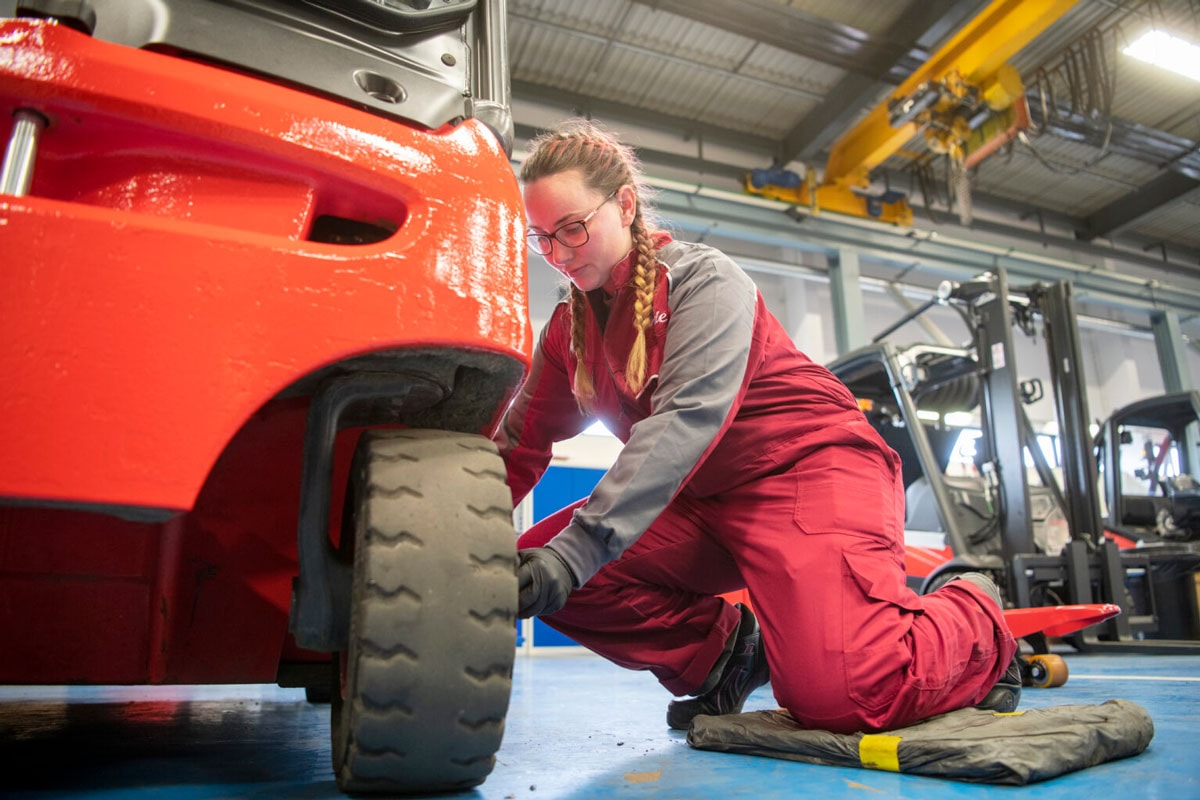
A. Age of the Forklift
Older forklifts generally need more frequent servicing. Over time, wear and tear can affect critical components, and consistent upkeep becomes essential to maintain safe, reliable operation.
B. Type of Forklift (Electric, Internal Combustion)
Electric forklifts typically have fewer moving parts and often require less maintenance compared to gas or diesel models. However, they do require regular battery checks, while internal combustion forklifts need periodic checks for engine oil, fuel filters, and exhaust systems.
C. Frequency of Use
Forklifts used extensively throughout the day will need more frequent inspections. High-use equipment is subject to greater wear, increasing the necessity for regular maintenance to ensure operational reliability.
D. Operating Environment
Whether the forklift is used indoors or outdoors significantly impacts its maintenance needs. Outdoor forklifts, exposed to dirt, dust, and moisture, are at higher risk for corrosion and damage, while indoor forklifts may require different attention based on warehouse conditions. Factoring these elements into a forklift maintenance schedule ensures that each forklift receives the proper care based on its specific working conditions.
Creating a Preventative Maintenance Plan
Developing a forklift maintenance plan is essential for preventing breakdowns and optimizing equipment lifespan. A well-structured plan begins by consulting both OSHA regulations and manufacturer guidelines, which provide key insights on safe operation and service requirements. OSHA emphasizes the importance of planned maintenance for workplace safety, which includes regular inspections and servicing based on each forklift’s specific usage and environment.
To set up an effective plan, begin by assessing how often to schedule forklift maintenance visits—typically every 500, 1,000, or 2,000 hours of operation, depending on forklift type and workload. Outline maintenance tasks for each interval, from daily and weekly checks to more in-depth monthly and quarterly inspections.
Using a logbook or digital tracking system helps ensure consistency and allows teams to monitor service history. This structured approach minimizes downtime, improves safety, and helps maintain reliable forklift performance over time.
Daily and Weekly Forklift Maintenance Checklist
Consistent daily and weekly maintenance checks play a significant role in keeping forklifts in top condition. Forklift operators should conduct pre-operational checks each day to ensure the machine is safe to use. Here’s a checklist for daily and weekly tasks to help prevent issues:
Daily Pre-Operational Checks:
- Tires – Inspect for proper inflation and wear to avoid stability issues.
- Brakes and Hand Brake – Ensure the brakes work smoothly, and the hand brake holds firmly.
- Hydraulic Oil Pump and System – Check hydraulic levels and inspect for any leaks or visible damage.
- Lights and Warning Signals – Test lights, horn, and warning alarms to maintain safe visibility and alert capabilities.
- Seat and Steering – Adjust the seat as needed and check the steering for proper control and response.
Weekly Maintenance Tasks:
- Fluid Levels – Inspect and top off hydraulic oil, transmission oil, and engine oil if necessary.
- Air Filter – Clean or replace the air filter to prevent engine strain.
- Battery (for electric forklifts) – Check the battery for charge levels and maintenance needs.
- Carriage Rollers and Mast Components – Inspect for alignment, wear, and signs of potential issues with lift mechanics.
Performing these regular maintenance tasks enables operators to catch potential issues early, keeping forklifts operational and safe for daily use.
6. Monthly and Quarterly Maintenance Tasks
Monthly and quarterly forklift maintenance visits ensure equipment stays in optimal working condition. These maintenance intervals address wear that daily and weekly checks may overlook, keeping the forklift reliable and safe for extended operation.
Monthly Tasks:
- Hydraulic Oil Levels – Check and top off hydraulic oil as needed, ensuring the system operates smoothly.
- Engine Oil and Filters – Inspect and replace oil filters, and change the engine oil if required to avoid engine strain.
- Battery (for electric forklifts) – Clean battery terminals and check electrolyte levels for better power efficiency.
- Brake Function – Test and adjust brakes, ensuring they provide consistent stopping power for safe operation.
Quarterly Tasks:
- Transmission and Fuel Systems – For internal combustion models, inspect transmission oil and fuel filters, replacing as needed.
- Mast Chains and Carriage Rollers – Inspect for wear or misalignment to prevent breakdowns.
- Cooling System – Ensure proper coolant levels and inspect the radiator for clogs or leaks.
Following these different maintenance intervals supports reliable performance and prevents wear from escalating into costly repairs.
Specific Service Needs by Forklift Type
Each forklift type has unique service needs that ensure optimal performance and longevity.
- Electric Forklifts: Electric forklifts generally require lower maintenance but depend heavily on their batteries. Regularly inspect battery terminals, maintain electrolyte levels, and keep batteries charged. Also, check the electrical system for any wiring or connection issues.
- Liquid Propane Forklifts: These forklifts run on propane tanks, which require secure mounting and leak checks. Regularly inspect fuel lines and connections for damage, and replace the fuel filter as needed to keep combustion smooth.
- Internal Combustion Forklifts: Gasoline or diesel-powered forklifts need frequent engine oil checks, fuel filter changes, and exhaust inspections. Engine air filters should also be checked and replaced periodically to prevent contaminants from damaging engine components.
By addressing proper maintenance specific to each forklift type, you ensure safety, efficiency, and reduced repair costs.
Avoiding Costly Repairs Through Preventative Maintenance
Preventative maintenance is essential for avoiding costly repairs that can arise from neglect. Regular service allows technicians to catch small issues before they escalate into expensive repairs that disrupt operations and increase downtime.
Routine maintenance—such as inspecting brakes, replacing worn parts, and ensuring proper fluid levels—keeps forklifts operating smoothly, minimizing the likelihood of sudden breakdowns. By adhering to a regular service schedule, you avoid emergency repairs that often cost far more than planned maintenance. Frequent service also extends the forklift’s lifespan, as well-maintained equipment handles wear more effectively over time. Investing in preventative maintenance is a cost-saving strategy that preserves equipment value, maintains productivity, and keeps operational expenses low in the long run.
Selecting the Right Forklift Service Provider
Choosing a reliable, professional service provider is essential for safe and effective forklift maintenance. Working with certified forklift technicians ensures that every service is performed accurately and aligns with industry safety standards. At Upright Forklift Repair in Houston and Humble, TX, we provide expert local forklift repair with a team of highly trained and certified technicians who understand the complexities of forklift maintenance across all models.
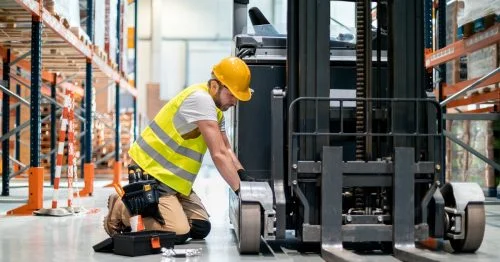
Our expertise means we’re equipped to handle everything from routine maintenance to in-depth repairs, ensuring your forklift fleet remains operational and safe. Upright Forklift Repair’s reputation in the Houston area reflects our commitment to top-tier service, quick response times, and a high level of customer satisfaction, making us a trusted choice for businesses across industries.
Can I Service My Forklift Myself?
While DIY maintenance may seem convenient, DIY forklift maintenance often lacks the precision required for optimal performance and safety. Forklifts are complex machines, and without specialized knowledge, attempting repairs can lead to serious safety hazards and operational issues.
Forklift repairs should always be handled by trained technicians who understand the intricacies of these machines and comply with occupational safety standards. Certified professionals ensure proper service, helping avoid accidents and costly errors that can arise from DIY attempts.
The Impact of Regular Maintenance on Safety and Efficiency
Routine maintenance plays a vital role in maintaining both safety and efficiency in the workplace. A well-maintained forklift contributes to improved safety by reducing the chances of equipment malfunctions that could lead to accidents. Consistent service ensures that forklifts remain in optimal performance condition, allowing operators to complete tasks smoothly and without interruption.
By mitigating safety hazards such as brake failure or hydraulic issues, regular maintenance protects not only the operator but also those working nearby. Additionally, forklifts that are routinely maintained experience less downtime, increasing productivity and supporting a more efficient workflow. Prioritizing maintenance is an investment in both employee safety and overall operational efficiency.
Conclusion and Call to Action
Regular forklift maintenance is key to maximizing equipment lifespan, safety, and efficiency. Following a structured forklift maintenance schedule prevents unexpected breakdowns and ensures optimal performance, which ultimately saves on costly repairs. For expert forklift service tailored to your needs in the Houston and Humble, TX, areas, contact Upright Forklift Repair today. Our certified technicians can help you set up a preventative maintenance plan that keeps your forklifts running smoothly and safely.