Forklift Repair and Maintenance: The Key to Efficient Operations
In the bustling landscape of industries and warehouses, forklifts stand as indispensable workhorses, facilitating the seamless movement of goods. Behind their efficiency lies a crucial element often overlooked—the significance of forklift maintenance. Let’s delve into the intricacies of this topic to grasp why comprehending forklift repair and service is paramount for Houston businesses.
The Backbone of Operations
Forklifts, akin to the backbone of many operations, play a pivotal role in ensuring the smooth flow of goods within a facility. Imagine the repercussions of a forklift breaking down amidst a busy workday—it not only disrupts the workflow but also incurs unforeseen costs and potential safety hazards.
Importance of Forklift Maintenance
- Operational Efficiency: Regular maintenance enhances a forklift’s operational efficiency, ensuring it performs at its peak, day in and day out.
- Cost Savings: Proactive maintenance minimizes the risk of major breakdowns, translating to substantial cost savings in the long run. A well-maintained forklift is less likely to succumb to unexpected repairs that can strain a business’s budget.
- Safety First: Beyond efficiency and cost considerations, forklift maintenance is fundamentally tied to safety. A well-maintained forklift is a safer forklift, reducing the likelihood of accidents that can have severe consequences for both personnel and inventory.
Why Understanding Forklift Repair and Service is Crucial for Businesses
Mitigating Downtime
- Strategic Planning: Understanding the nuances of forklift repair allows businesses to strategize and plan maintenance activities, minimizing operational downtime.
- Downtime Costs: Every minute a forklift is out of commission translates to potential losses. Knowledgeable businesses can implement preventive measures, reducing the frequency and duration of downtime.
Ensuring Longevity
- Investment Protection: Forklifts represent a substantial investment for businesses. Knowledge of repair and service ensures that this investment is protected, extending the lifespan of the equipment.
- Maximizing ROI: By comprehending the intricacies of forklift maintenance, businesses can extract maximum return on investment (ROI) from their equipment, optimizing its performance over the long term.
Forklift maintenance is not merely a routine task; it’s a strategic imperative. The following sections will unravel the mysteries of forklift repair, service timelines, and the critical components that keep these essential machines in prime condition. Join us on this journey to empower your business with the knowledge it needs to navigate the complex terrain of forklift maintenance successfully.
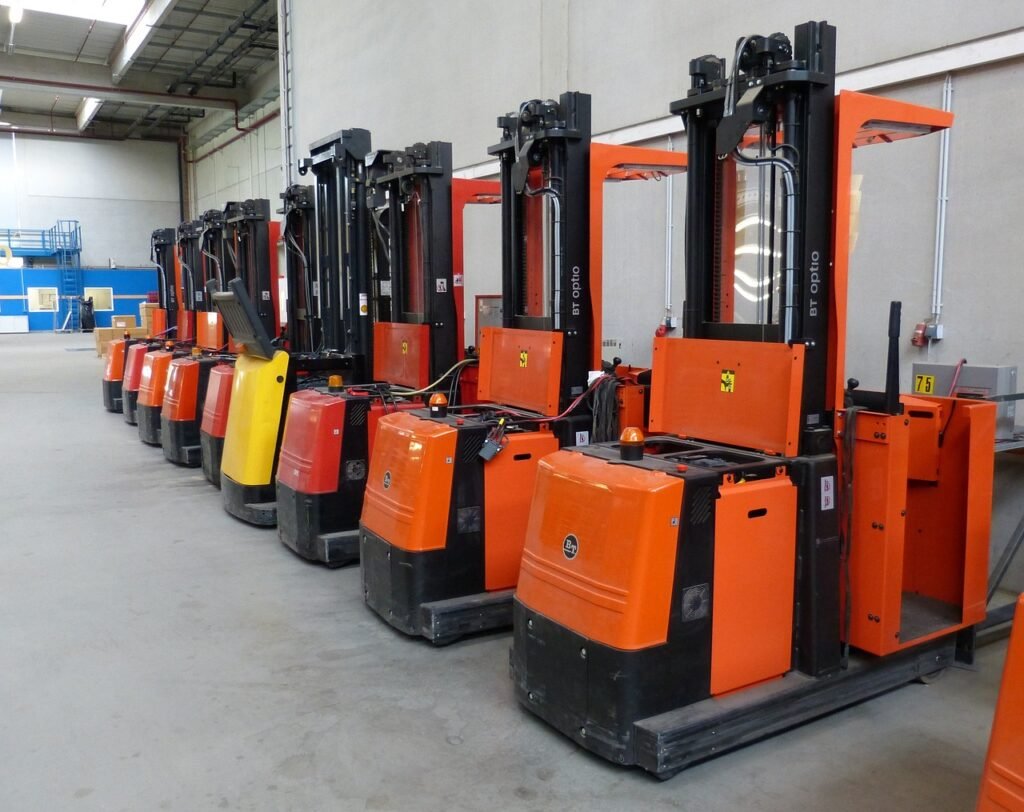
Are Forklifts Easy to Repair?
Maintaining and repairing forklifts can vary in complexity based on the specific issue and the model of the forklift. Routine maintenance tasks, such as changing fluids and inspecting parts, are generally straightforward and can be performed with basic mechanical knowledge.
However, more complex repairs, such as addressing electrical issues or major engine problems, may require specialized skills and expertise. In such cases, it’s advisable to consult with a certified forklift technician or a professional service provider.
Regularly servicing your forklift and addressing minor issues promptly can contribute to its longevity and reduce the likelihood of major repairs. Additionally, following the manufacturer’s maintenance guidelines and seeking professional assistance when needed can help ensure the forklift remains in optimal working condition.
Factors Influencing Ease of Repair
Understanding the repairability of forklifts requires delving into various factors that influence the process. This insight aids businesses in making informed decisions about their maintenance strategies.
1. Complexity of Design
- Forklifts, with their intricate design, can vary in complexity. The more intricate the design, the more challenging the repair process.
2. Availability of Parts
- The ease of repair is closely tied to the availability of replacement parts. Forklift models with readily available parts are generally easier to repair.
3. Technology Integration
- Forklifts with advanced technological features might demand specialized knowledge for repair. Compatibility with diagnostic tools can simplify the troubleshooting process.
Common Issues and Troubleshooting Tips
Knowing the common issues that forklifts encounter empowers businesses to address potential problems proactively. Here are some prevalent issues and tips for troubleshooting:
1. Battery Issues
- Issue: Forklift not starting.
- Tip: Regularly check and maintain the battery. Clean terminals and ensure proper charging.
2. Hydraulic Problems
- Issue: Unusual noises or difficulty in lifting loads.
- Tip: Inspect hydraulic fluid levels, hoses, and connections. Address leaks promptly.
3. Brake Malfunctions
- Issue: Inconsistent braking.
- Tip: Regularly inspect brake systems and address any signs of wear or malfunction promptly.
Importance of Regular Maintenance to Prevent Major Repairs
Prevention is often more cost-effective than cure, and the same holds true for forklifts. Regular maintenance serves as a proactive approach to prevent major repairs and ensures the longevity of the equipment.
1. Scheduled Inspections
- Conducting routine inspections allows businesses to identify potential issues before they escalate, reducing the likelihood of major breakdowns.
2. Lubrication and Cleaning
- Regularly lubricating moving parts and keeping the forklift clean can prevent premature wear and tear, contributing to overall ease of maintenance.
3. Operator Training
- Well-trained forklift operators can contribute significantly to the prevention of damages. Providing comprehensive training on proper usage and reporting procedures is crucial.
The ease of forklift repair is influenced by a combination of design complexity, parts availability, and technological integration. Businesses can enhance this ease by addressing common issues promptly and embracing a proactive maintenance approach. The next segment will explore the time considerations involved in forklift repairs, shedding light on how swiftly businesses can get their essential equipment back in operation.
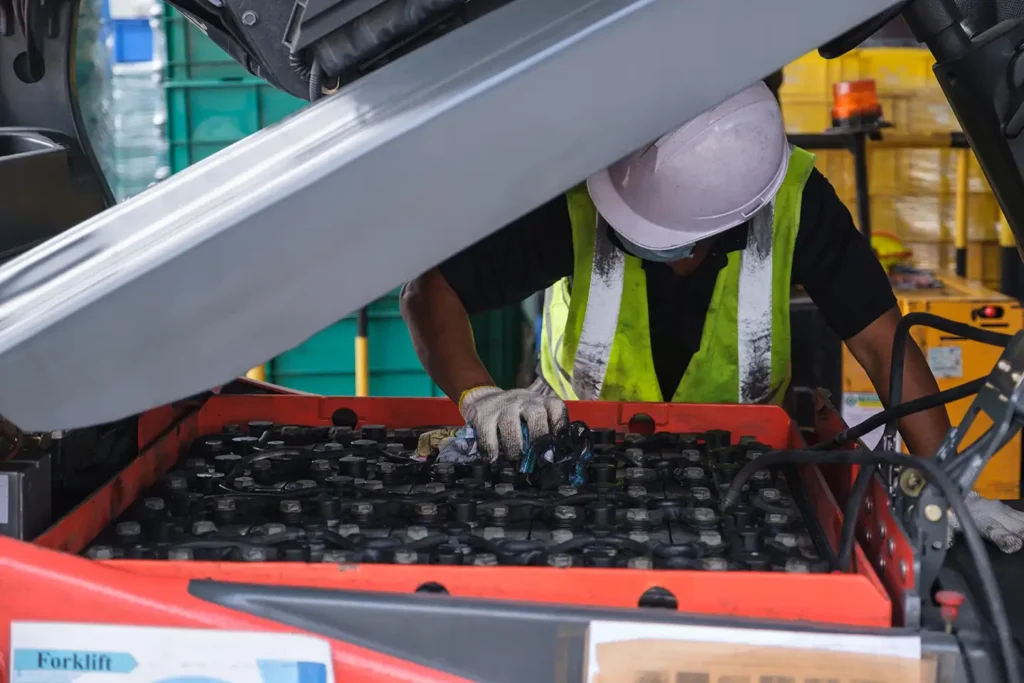
How Long Does It Take to Repair a Forklift?
The time required to repair a forklift depends on the nature and extent of the issue. Simple repairs or routine maintenance tasks, such as changing fluids or replacing minor components, can often be completed within a few hours.
More complex repairs, such as addressing intricate electrical problems or significant engine issues, may take longer. In such cases, the repair process could extend to a day or more, depending on the availability of replacement parts and the complexity of the repair work.
The efficiency of the repair process also depends on the expertise of the technician performing the repairs. A skilled and experienced forklift technician may diagnose and fix issues more quickly than someone with less experience.
To minimize downtime and ensure a swift resolution, it’s advisable to communicate with the repair technician, obtain a clear estimate of the repair time, and inquire about any factors that might affect the timeline, such as parts availability or the need for additional diagnostics.
Overview of Repair Time Variability
Understanding the duration of forklift repairs is essential for businesses aiming to minimize downtime and maintain operational efficiency. The variability in repair times stems from several factors, each contributing to the overall timeframe.
1. Nature of the Issue
- Simple issues like a battery replacement may take a shorter time compared to complex hydraulic system repairs. The nature of the problem directly influences repair duration.
2. Availability of Parts
- Repair times are heavily dependent on the availability of necessary parts. Quick access to components can significantly reduce the overall repair timeframe.
3. Skill and Experience of the Technician
- The expertise of the technician performing the repair is a crucial factor. A skilled and experienced technician can diagnose and address issues more efficiently.
Factors Affecting Repair Duration
To delve deeper into the nuances of repair duration, it’s essential to explore the factors that directly impact the time it takes to bring a forklift back to operational status.
1. Diagnostic Phase
- The initial diagnostic phase, where the technician identifies the root cause of the problem, can vary in duration based on the complexity of the issue.
2. Parts Procurement
- If replacement parts are required, the time spent procuring these components can significantly impact the overall repair duration. Efficient supply chain management is crucial.
3. Technician Workload
- The workload of the technician and the availability of skilled personnel can influence repair times. High-demand periods may result in longer waiting times for repairs.
Tips for Minimizing Downtime During Forklift Repairs
Businesses can take proactive measures to minimize downtime during forklift repairs, ensuring swift resolutions and reduced operational disruptions.
1. Regular Maintenance Schedules
- Adhering to regular maintenance schedules can prevent potential issues, reducing the frequency and urgency of repairs.
2. Stocking Essential Parts
- Maintaining an inventory of essential forklift parts on-site can expedite the repair process by eliminating delays associated with parts procurement.
3. Collaboration with Skilled Service Providers
- Establishing partnerships with skilled forklift service providers ensures quick access to experienced technicians when repairs are needed.
The time required to repair a forklift is a multifaceted aspect influenced by the nature of the issue, availability of parts, and the expertise of the technician. By understanding these factors and implementing proactive measures, businesses can minimize downtime and keep their forklifts in optimal working condition. The subsequent section will delve into the systematic servicing of forklifts, providing insights into best practices for maintaining these crucial pieces of equipment.
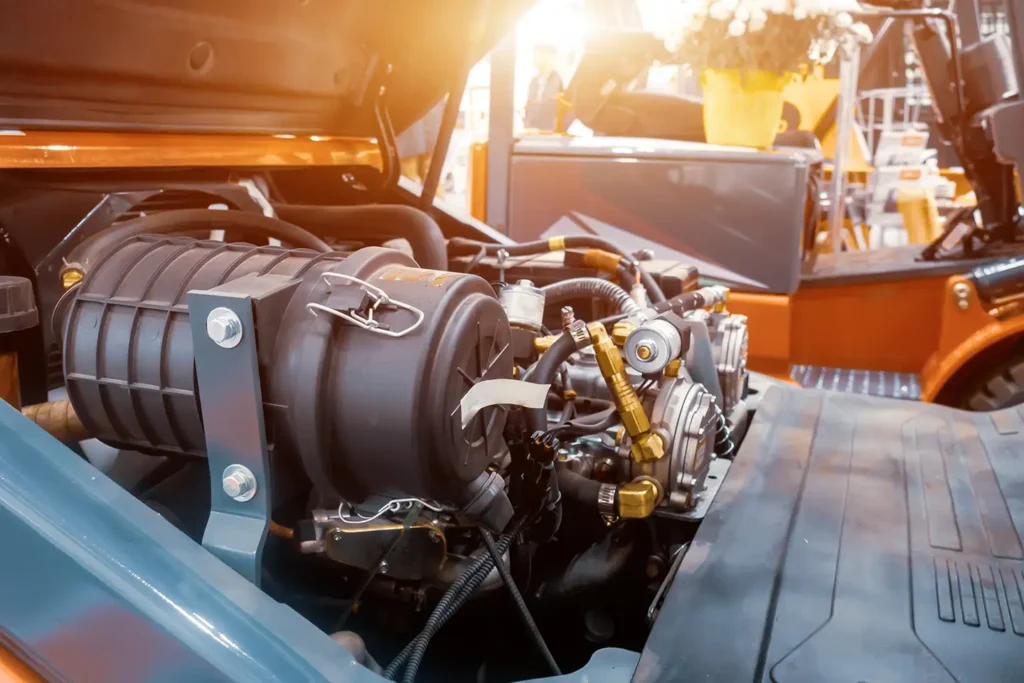
How Do You Service a Forklift?
Servicing a forklift involves regular maintenance tasks to ensure optimal performance. This includes checking and changing fluids, inspecting and lubricating moving parts, examining the braking system, and assessing the overall condition of the forklift. Additionally, it’s crucial to follow the manufacturer’s guidelines for scheduled maintenance and address any identified issues promptly to prevent major repairs. Regular servicing not only enhances the forklift’s lifespan but also contributes to a safer and more efficient operation.
Importance of Regular Servicing
Regular servicing is the cornerstone of forklift maintenance, ensuring optimal performance, longevity, and safety. Understanding the significance of this routine practice is vital for businesses relying on forklifts in their daily operations.
1. Enhanced Performance
- Regular servicing addresses wear and tear, keeping the forklift’s components in top condition and optimizing overall performance.
2. Extended Lifespan
- Routine servicing prevents premature aging of critical parts, contributing to the extension of the forklift’s lifespan and protecting the business’s investment.
3. Safety Assurance
- Servicing includes thorough inspections of safety-critical components, reducing the risk of accidents and ensuring a safe working environment.
Step-by-Step Guide to Basic Forklift Servicing
Conducting basic forklift servicing doesn’t necessarily require advanced technical skills. This step-by-step guide simplifies the process for businesses looking to incorporate regular servicing into their maintenance routine.
1. Pre-Service Inspection
- Begin with a visual inspection of the forklift. Check for any visible damages, leaks, or loose components.
2. Fluid Level Check
- Inspect and, if necessary, top up fluids such as hydraulic oil, brake fluid, and coolant.
3. Battery Maintenance
- Clean battery terminals, check water levels (if applicable), and ensure proper charging.
4. Tire Inspection
- Inspect tires for wear, damage, and proper inflation. Replace or rotate tires as needed.
5. Brake System Check
- Test and inspect the brake system for responsiveness. Address any issues promptly.
6. Lubrication
- Lubricate moving parts, including hinges and forks, to reduce friction and wear.
7. Filter Replacement
- Replace air and fuel filters at recommended intervals to maintain optimal engine performance.
Professional Servicing vs. DIY Options
Deciding between professional servicing and DIY options depends on factors like the complexity of the task, available resources, and the expertise of personnel.
1. Professional Servicing
- Pros: Expertise, comprehensive inspections, adherence to manufacturer recommendations.
- Cons: Cost implications, scheduling dependencies.
2. DIY Options
- Pros: Cost-effective, flexibility in scheduling.
- Cons: Limited expertise, potential oversight of critical issues.
Ultimately, the choice between professional servicing and DIY options should align with the specific needs and resources of the business.
Regular forklift servicing is a proactive measure essential for maintaining peak performance, ensuring safety, and extending the equipment’s lifespan. The subsequent section will delve into the financial aspects of forklift maintenance by exploring the most expensive parts and strategies for cost-effective replacements.
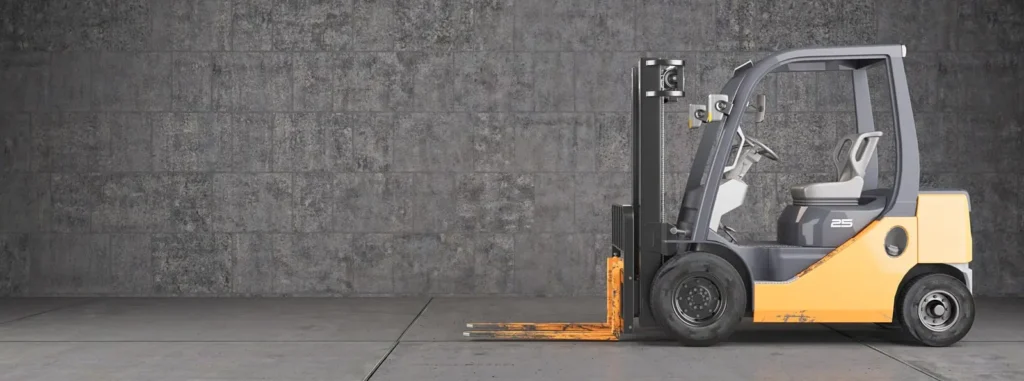
What Is the Most Expensive Part of a Forklift?
The costliest component to replace in a forklift is often the hydraulic system, specifically the hydraulic pump and cylinder. This system is critical for the forklift’s lifting and tilting functions. Repairs or replacements to the hydraulic components can be relatively expensive due to the precision and complexity involved. Regular maintenance and prompt attention to any hydraulic issues can help prevent major breakdowns and mitigate potential high costs associated with this crucial system.
Breakdown of Forklift Components and Costs
Understanding the cost dynamics of forklift components is crucial for businesses managing maintenance budgets. Let’s break down the key components and associated costs that contribute to the overall expense of forklift ownership.
1. Engine Components
- Costs: Engine repairs or replacements can be significant, encompassing components like the cylinder head, pistons, and fuel system.
2. Hydraulic System
- Costs: Hydraulic pumps, cylinders, and hoses can contribute to high repair expenses if not properly maintained.
3. Transmission
- Costs: Repairing or replacing the transmission can be a substantial investment, including costs for parts like the gearbox and clutch.
4. Mast and Forks
- Costs: Mast and fork repairs involve expenses related to the lifting mechanism, chains, and forks themselves.
Identifying the Most Expensive Parts
Not all forklift components have equal financial implications. Identifying the most expensive parts is essential for businesses aiming to allocate resources effectively.
1. Engine
- The engine is often one of the costliest components due to the complexity of its parts and the critical role it plays in overall forklift performance.
2. Hydraulic System
- The hydraulic system, crucial for lifting and lowering loads, can entail significant costs if neglected or improperly maintained.
3. Transmission
- The transmission, responsible for regulating power to the wheels, is another area where repairs can lead to substantial expenses.
Strategies for Cost-Effective Forklift Part Replacements
Navigating the financial aspects of forklift maintenance requires strategic approaches to ensure cost-effectiveness without compromising performance.
1. Regular Maintenance
- Proactive, regular maintenance helps identify and address issues before they escalate, reducing the likelihood of expensive component failures.
2. Quality Replacement Parts
- Opting for quality replacement parts, though an initial investment, often proves cost-effective in the long run by enhancing reliability and longevity.
3. Strategic Budgeting
- Developing a comprehensive maintenance budget and allocating resources strategically can help businesses plan for and manage the costs of forklift repairs.
Understanding the breakdown of forklift components and costs, identifying the most expensive parts, and implementing cost-effective replacement strategies are essential aspects of managing forklift maintenance expenses. The subsequent section will explore the lifespan of a forklift, shedding light on factors that influence its longevity and performance over time.
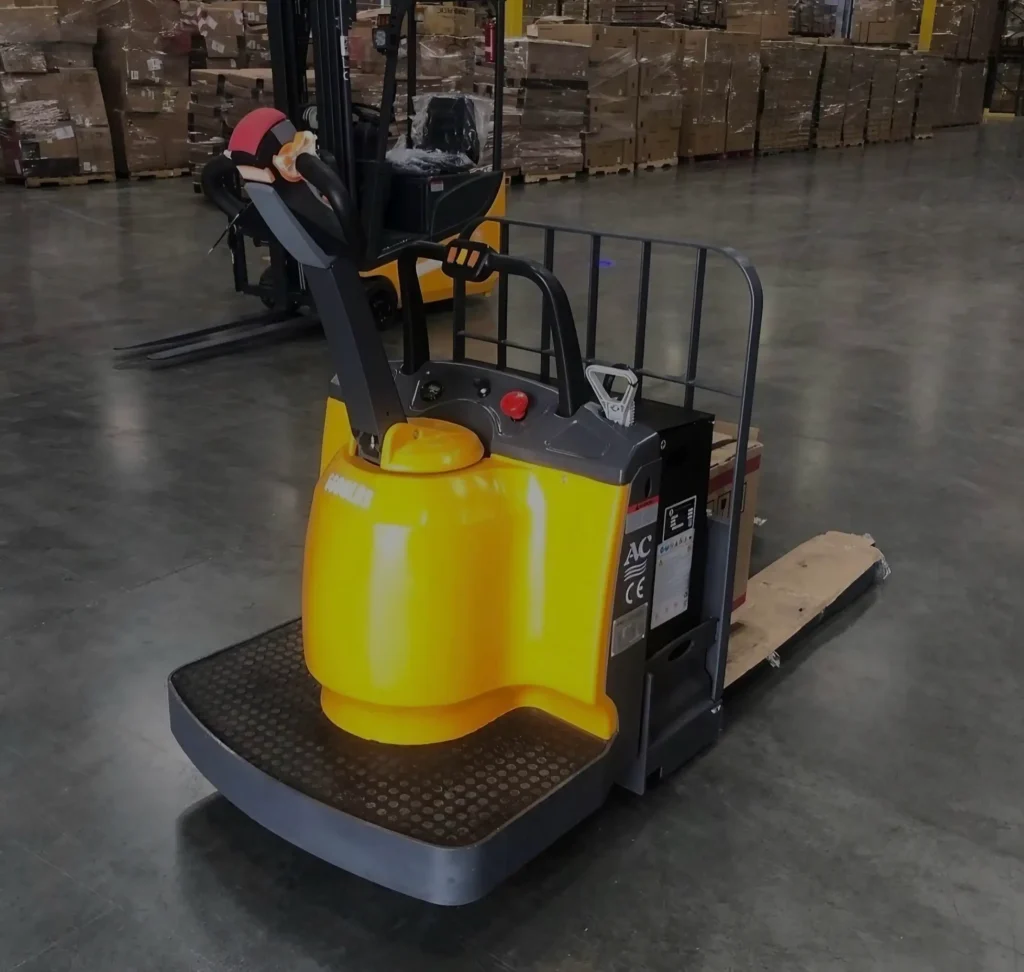
What Is the Lifespan of a Forklift?
The lifespan of a forklift varies based on factors such as usage, maintenance, and the operating environment. Generally, a well-maintained forklift can last anywhere from 10,000 to 20,000 hours of operation. This equates to roughly 8 to 10 years for a standard 2,000 hours per year usage.
Factors that influence lifespan include adherence to regular maintenance schedules, proper training for operators, and the intensity of use. Forklifts used in heavy-duty operations may experience more wear and require more frequent maintenance.
Regularly monitoring and addressing issues promptly, along with following the manufacturer’s recommended maintenance guidelines, can contribute to extending the lifespan of a forklift and optimizing its performance throughout its operational years.
Factors Influencing Forklift Lifespan
Understanding the lifespan of a forklift involves considering various factors that influence its longevity and overall performance throughout its operational life.
1. Usage Intensity
- Forklifts subjected to heavy daily use may have a shorter lifespan compared to those used intermittently. High-intensity operations contribute to faster wear and tear.
2. Maintenance Practices
- Rigorous adherence to regular maintenance schedules significantly influences the lifespan of a forklift. Well-maintained forklifts tend to endure longer, providing optimal performance over time.
3. Environment
- Operating conditions, such as exposure to extreme temperatures, dust, and corrosive materials, can impact the forklift’s components and contribute to its overall wear.
4. Technological Advances
- Technological advancements in forklift design and engineering may influence the perceived obsolescence of older models, affecting their lifespan from a functional and operational standpoint.
Importance of Proper Maintenance in Extending Lifespan
Proper maintenance emerges as a pivotal factor in extending the lifespan of a forklift, ensuring that it remains a reliable and cost-effective asset for businesses.
1. Preventive Inspections
- Regular, preventive inspections identify potential issues before they escalate, preventing premature wear and addressing concerns proactively.
2. Scheduled Servicing
- Adhering to scheduled servicing, including lubrication, fluid checks, and component replacements, contributes to the overall health of the forklift and prolongs its operational life.
3. Timely Repairs
- Addressing issues promptly, even minor ones, prevents them from evolving into major problems that could significantly impact the forklift’s performance and longevity.
Signs That a Forklift May Be Reaching the End of Its Life
Recognizing indicators that a forklift is approaching the end of its operational life is crucial for businesses to make informed decisions about replacement or extensive repairs.
1. Increased Repair Frequency
- A noticeable uptick in repair frequency may suggest that the forklift is reaching a point where repairs become financially unsustainable.
2. Decreased Performance
- Gradual deterioration in performance, such as reduced lifting capacity or slower operation, can signal that the forklift’s essential components are wearing out.
3. Obsolete Technology
- As newer, more advanced forklift models enter the market, older models may become obsolete, influencing their operational relevance and potential for continued maintenance.
The lifespan of a forklift is influenced by a combination of factors, including usage intensity, maintenance practices, environmental conditions, and technological advances. Proper maintenance emerges as a key strategy for businesses aiming to maximize the longevity of their forklifts. The next section will delve into the most replaced parts on forklifts, shedding light on components that frequently require attention and replacement during the course of a forklift’s operational life.
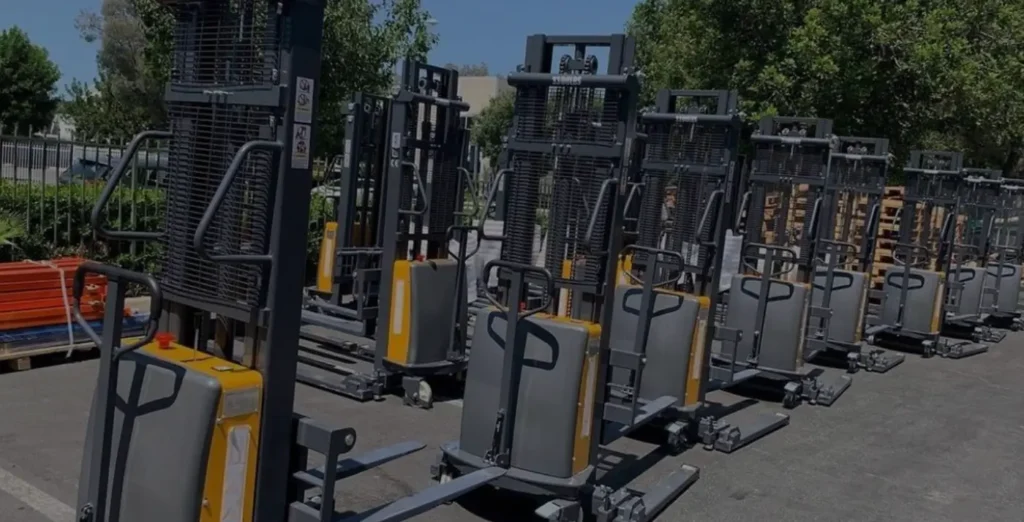
What Are the Most Replaced Parts on Forklifts?
Commonly replaced parts on forklifts include tires, brakes, and hydraulic components such as seals and hoses. Forklift tires, especially those on the front wheels, endure significant wear and tear and may need replacement due to damage or regular use. Brake systems, essential for safety, are also subject to frequent replacement.
Hydraulic components, including seals and hoses, are crucial for the lifting and tilting functions of a forklift. Due to their constant movement and exposure to pressure, these parts may wear out over time and require replacement. Regular inspections, prompt maintenance, and addressing minor issues can help extend the life of these components and minimize the frequency of replacements.
Analysis of Commonly Replaced Forklift Components
Understanding the components that frequently require replacement is integral to developing a proactive and cost-effective forklift maintenance strategy.
1. Forklift Tires
- Analysis: Forklift tires bear the brunt of heavy loads, leading to frequent wear and tear.
2. Brake Components
- Analysis: The constant stopping and starting in typical forklift operations contribute to the regular replacement of brake pads, discs, and related components.
3. Filters
- Analysis: Air and fuel filters, crucial for maintaining the forklift’s engine performance, are commonly replaced due to their regular wear and clogging.
4. Hydraulic Components
- Analysis: Hydraulic system components, including hoses and seals, are prone to wear, particularly in forklifts used for heavy lifting.
5. Batteries
- Analysis: Forklift batteries undergo significant stress during daily operations, leading to eventual degradation and the need for replacement.
Tips for Proactive Replacement to Avoid Breakdowns
Proactive replacement of certain forklift components can help businesses avoid unexpected breakdowns and maintain operational continuity.
1. Scheduled Tire Inspections
- Regularly inspecting tires for wear and damage allows for proactive replacement before issues escalate, minimizing the risk of unexpected failures.
2. Routine Brake System Checks
- Implementing routine checks of the brake system ensures early detection of wear, enabling timely replacement and preventing safety hazards.
3. Filter Replacement Timelines
- Adhering to recommended timelines for filter replacements prevents clogging and ensures optimal engine performance.
4. Hydraulic System Maintenance
- Regularly maintaining the hydraulic system, including inspections and fluid replacements, minimizes wear and the need for premature component replacement.
5. Battery Health Monitoring
- Implementing a battery health monitoring program helps identify deterioration in advance, allowing for timely replacement and avoiding disruptions in operation.
Cost Considerations in Routine Forklift Maintenance
While proactive replacement is crucial, businesses must also consider the financial aspects of routine forklift maintenance to ensure cost-effectiveness.
1. Quality Replacement Parts
- Opting for high-quality replacement parts may have a higher upfront cost but often proves cost-effective in the long run by reducing the frequency of replacements.
2. Strategic Budgeting
- Developing a comprehensive maintenance budget and allocating resources strategically ensures that businesses can address necessary replacements without exceeding financial constraints.
3. Professional Consultation
- Seeking professional consultation can aid businesses in developing a tailored maintenance strategy, optimizing costs while ensuring the longevity of forklift components.
Understanding the commonly replaced parts on forklifts, proactively addressing replacements, and considering cost-effective maintenance practices contribute to a comprehensive approach to forklift maintenance. The subsequent section will explore one of the most serious forklift defects, shedding light on the potential consequences and strategies for prevention.
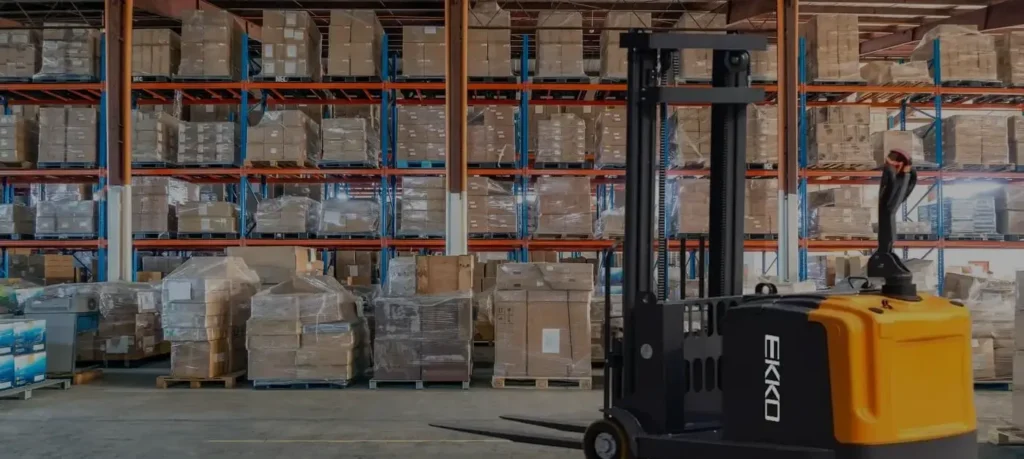
What Is One of the Most Serious Forklift Defects?
One of the most serious forklift defects involves issues with the braking system. Brake failures or malfunctions can pose significant safety risks in the workplace. Inadequate braking capability can lead to accidents, collisions, and injuries. Regular inspections of the forklift’s braking system, including the brake fluid, pads, and overall functionality, are essential to identify and address defects promptly. Ensuring the proper functioning of the braking system is crucial for maintaining a safe working environment and preventing potentially severe accidents involving forklifts.
Identification of Critical Forklift Defects
Understanding and identifying critical defects in forklifts is paramount for ensuring both safety and operational efficiency.
1. Faulty Braking Systems
- Identification: Issues with brakes, such as delayed response or uneven braking, pose a serious defect.
2. Hydraulic System Failures
- Identification: Leaks, reduced lifting capacity, or erratic movements during lifting indicate potential hydraulic system defects.
3. Steering System Malfunctions
- Identification: Difficulty in steering, unusual noises, or erratic movements point to defects in the steering system.
Impact of Serious Defects on Safety and Performance
Serious defects in forklifts can have far-reaching consequences, affecting both the safety of operators and the overall performance of the equipment.
1. Safety Hazards
- Impact: Faulty brakes, hydraulic failures, or steering malfunctions can result in accidents, posing severe safety hazards for operators and bystanders.
2. Operational Disruptions
- Impact: Serious defects can lead to unexpected breakdowns, causing disruptions in operations and affecting productivity.
3. Potential Damage to Goods
- Impact: Defects in forklifts may lead to mishandling of loads, potentially damaging goods and impacting inventory.
Strategies for Early Detection and Prevention
Early detection and prevention of serious defects are key components of a proactive forklift maintenance strategy.
1. Regular Inspections
- Conducting routine inspections, including thorough checks of brakes, hydraulics, and steering components, allows for early detection of potential defects.
2. Operator Training
- Providing comprehensive training to forklift operators on identifying and reporting potential defects ensures timely intervention.
3. Data Analytics and Telematics
- Utilizing data analytics and telematics can provide insights into the health of forklift components, facilitating early detection of issues before they escalate.
4. Scheduled Maintenance Programs
- Implementing scheduled maintenance programs, including specific checks for critical components, helps prevent defects and ensures optimal forklift performance.
One of the most serious forklift defects involves issues with the braking, hydraulic, or steering systems. The impact of such defects extends beyond safety concerns to operational disruptions and potential damage to goods. By adopting strategies for early detection and prevention, businesses can mitigate these risks and maintain a safe and efficient forklift fleet. The final section will address the frequency at which forklift forks should be replaced, providing insights into proper maintenance practices for this essential component.
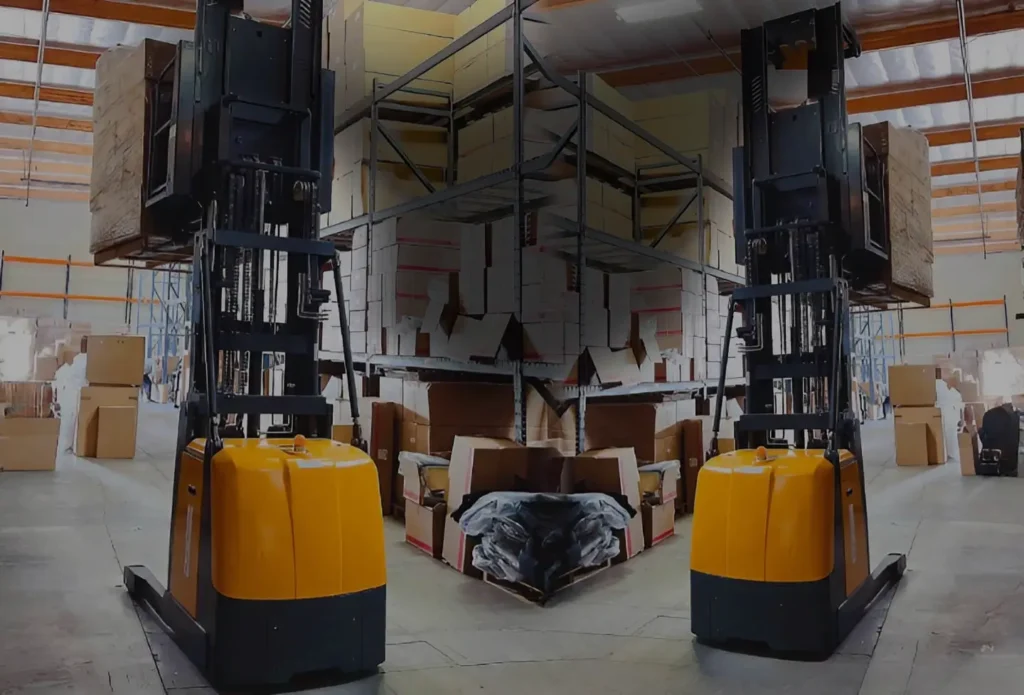
How Often Should Forklift Forks Be Replaced?
The frequency of forklift fork replacement depends on various factors, including usage, load weight, and operating conditions. As a general guideline, forklift forks should be inspected regularly, and replacement may be necessary when there is noticeable wear, bending, or damage that could compromise their structural integrity.
In high-use environments or when handling heavy loads, forks may need replacement more frequently. Regular visual inspections and adherence to the manufacturer’s guidelines for fork maintenance and replacement are crucial. It’s recommended to consult with a qualified technician or follow the manufacturer’s recommendations to determine the appropriate replacement schedule based on the specific conditions in which the forklift operates.
1. Load Stability
- Properly functioning forks contribute to load stability, ensuring that goods are securely lifted and transported without the risk of slippage or accidents.
2. Operator Safety
- Well-maintained forks contribute to operator safety by reducing the likelihood of load mishandling, preventing potential injuries, and creating a safer working environment.
3. Efficient Material Handling
- Forklift forks, when in optimal condition, facilitate efficient material handling, minimizing delays in operations and enhancing overall productivity.
Factors Influencing Fork Replacement Frequency
The frequency at which forklift forks should be replaced depends on various factors, with a key criterion being the height difference between the tips of the forks.
1. Height Difference Criterion
- Forks need replacement if the difference between the height of each tip exceeds 3% of the length of the blade. For instance, in a 48-inch blade, the height difference should not be greater than 1.44 inches.
2. Usage Intensity
- Fork replacement frequency may increase with higher usage intensity, especially in heavy-duty operations where forks undergo more stress and wear.
3. Material Composition
- The material composition of the forks, considering factors like strength and durability, influences how well they withstand the demands of lifting and transporting loads.
Fork Inspection and Maintenance Best Practices
Regular inspections and maintenance practices are crucial for ensuring the longevity and optimal performance of forklift forks.
1. Visual Inspections
- Regularly inspect forks for signs of wear, cracks, or deformities. Visual inspections can help identify issues early on.
2. Height Difference Measurement
- Measure the height difference between the tips of the forks regularly, adhering to the recommended criterion, to determine if replacement is necessary.
3. Material Handling Training
- Train forklift operators on proper material handling techniques to minimize stress on the forks and prevent premature wear.
4. Timely Replacement
- Replace forks promptly when they meet the height difference criterion, ensuring continued load stability and operator safety.
The proper functioning of forklift forks is integral to efficient material handling, load stability, and operator safety. Adhering to recommended height difference criteria and implementing regular inspections and maintenance practices are essential for determining when forks should be replaced and ensuring the longevity of this critical forklift component.
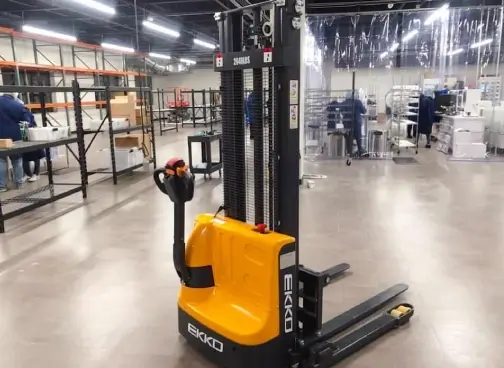
How Do Forklift Forks Get Damaged?
Forklift forks can sustain damage through various factors such as overloading beyond their rated capacity, improper use, or contact with hard surfaces like pallets or the ground. Impact from collisions, dragging loads, or uneven surfaces can lead to bending or distortion of the forks. Additionally, lack of proper maintenance, such as regular inspections for wear and tear, can contribute to unnoticed damage over time. It’s crucial for operators to follow safety guidelines, conduct routine inspections, and avoid exceeding the forklift’s load capacity to prevent damage to the forks and ensure safe and efficient operation.
Incorrect Chain Adjustments
- Issue: Incorrectly adjusted chains can place undue stress on the forks, leading to misalignments, bending, or structural damage.
Using the Fork More Than Its Rated Capacity
- Issue: Exceeding the rated capacity of the forks can lead to overloading, causing them to weaken, deform, or even break under the excessive weight.
Driving the Forklift While Holding Forks to the Ground
- Issue: Driving with forks in a lowered position creates friction and resistance, resulting in accelerated wear and potential damage to the fork tips.
Hoisting Big Objects with a Lifting Chain Attached to a Single Fork
- Issue: Lifting large objects with a chain attached to only one fork can cause uneven distribution of weight, leading to structural imbalances and potential bending.
Using Forks to Pick Up Loads That Are Too Far Out
- Issue: Extending the forks too far beyond their recommended capacity compromises stability, increasing the risk of tip-overs and structural damage.
Stress-Causing Attachments for the Forks
- Issue: Adding attachments that induce stress on the forks, without proper consideration of their load-bearing capacity, can lead to structural fatigue and damage.
Minor Mishaps
- Issue: Accidental collisions, impacts with obstacles, or mishandling during material handling operations can result in dents, bends, or other forms of damage.
Wear from Regular Use
- Issue: Regular use, especially in heavy-duty operations, subjects forks to gradual wear. Over time, this wear can accumulate, affecting the structural integrity of the forks.
Preventive Measures and Best Practices
To mitigate the risk of fork damage, businesses can adopt preventive measures and best practices in forklift operation.
1. Regular Inspections
- Conduct routine inspections to identify signs of wear, misalignments, or structural issues before they escalate.
2. Operator Training
- Provide comprehensive training to forklift operators on proper handling techniques and load capacities to avoid misuse and overloading.
3. Proper Fork Usage
- Use forks only for their intended purpose and within designated load capacities to prevent unnecessary stress and damage.
4. Attachment Compatibility Checks
- Ensure that any attachments used with the forks are compatible and do not induce excessive stress that could compromise structural integrity.
5. Immediate Repairs
- Address minor damages promptly through repairs to prevent them from escalating into more severe issues.
Understanding the factors that contribute to forklift fork damage empowers businesses to implement preventive measures and promote safe and efficient material handling practices. Regular maintenance, operator training, and adherence to usage guidelines are essential components of a comprehensive approach to forklift fork care and longevity.
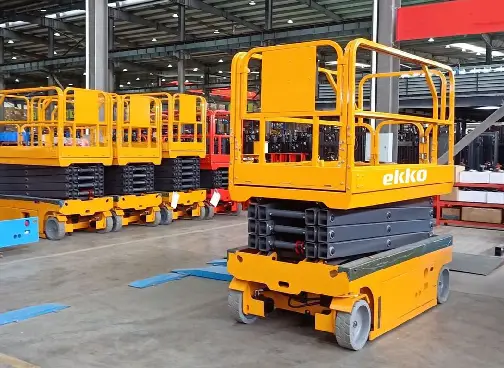
Conclusion
Summary of Key Takeaways
In delving into the intricacies of forklift maintenance, we’ve uncovered crucial insights that businesses, especially those reliant on forklifts, should consider. Let’s recap the key takeaways:
1. Forklift Maintenance Essentials
- Regular maintenance is the cornerstone of forklift longevity, encompassing aspects like tire care, brake system checks, and hydraulic system maintenance.
2. Repair Time Considerations
- The time required for forklift repairs varies based on factors such as the nature of the issue, availability of parts, and the skill of the technician.
3. Systematic Forklift Servicing
- Proper servicing involves a step-by-step approach, including pre-service inspections, fluid level checks, and scheduled component replacements.
4. Identifying Expensive Parts
- Understanding the costs associated with forklift components, particularly the engine, hydraulic system, and transmission, aids in budgeting and strategic maintenance planning.
5. Forklift Lifespan Factors
- Forklift lifespan is influenced by usage intensity, maintenance practices, environmental conditions, and technological advancements.
6. Most Replaced Parts
- Forklift tires, brake components, filters, hydraulic parts, and batteries are commonly replaced, emphasizing the need for proactive maintenance.
7. Serious Forklift Defects
- Defects in crucial systems such as brakes, hydraulics, and steering can pose safety hazards and disrupt operational efficiency.
8. Fork Replacement Frequency
- Forks should be replaced if the height difference between their tips exceeds 3% of the blade length, ensuring continued load stability.
9. Common Causes of Fork Damage
- Forks can be compromised by factors like incorrect chain adjustments, overloading, driving with forks to the ground, and using them beyond their capacity.
Encouragement for Proactive Forklift Maintenance
As we conclude this exploration into forklift maintenance, it’s evident that proactive care is the linchpin for optimal performance, safety, and longevity. Here’s a call to action:
1. Invest in Regular Inspections and Maintenance
- Routine inspections and scheduled maintenance are investments that pay off in enhanced forklift reliability and reduced long-term costs.
2. Prioritize Operator Training
- Well-trained operators contribute significantly to the prevention of defects and mishandling, fostering a culture of safety and operational efficiency.
3. Embrace Technological Advancements
- Explore the integration of telematics and data analytics to gain insights into forklift health, enabling informed decision-making and early defect detection.
Closing Thoughts on Optimizing Forklift Performance and Longevity
In optimizing forklift performance and longevity, businesses stand to gain not only in operational efficiency but also in cost-effectiveness and safety. As the backbone of material handling operations, forklifts deserve meticulous care and attention.
Let’s embark on a journey of proactive maintenance, embracing the wealth of knowledge shared here to elevate forklift operations to new heights. By doing so, businesses can navigate the complexities of forklift care with confidence, ensuring these indispensable machines remain reliable assets in their daily operations.