Forklift downtime occurs when equipment is out of operation due to mechanical failure or necessary repairs, disrupting a business’s productivity. When forklifts are idle, companies face increased repair costs, operating costs, and maintenance costs. This downtime not only delays material handling but also leads to bottlenecks in operations. Every minute of downtime translates into lost revenue and higher expenses.
For example, while addressing the repair costs associated with malfunctioning forklifts, businesses also face ongoing operating costs such as employee wages for idle time. Additionally, recurring maintenance costs from frequent breakdowns strain budgets. Minimizing downtime is crucial for maintaining smooth operations and keeping costs under control.
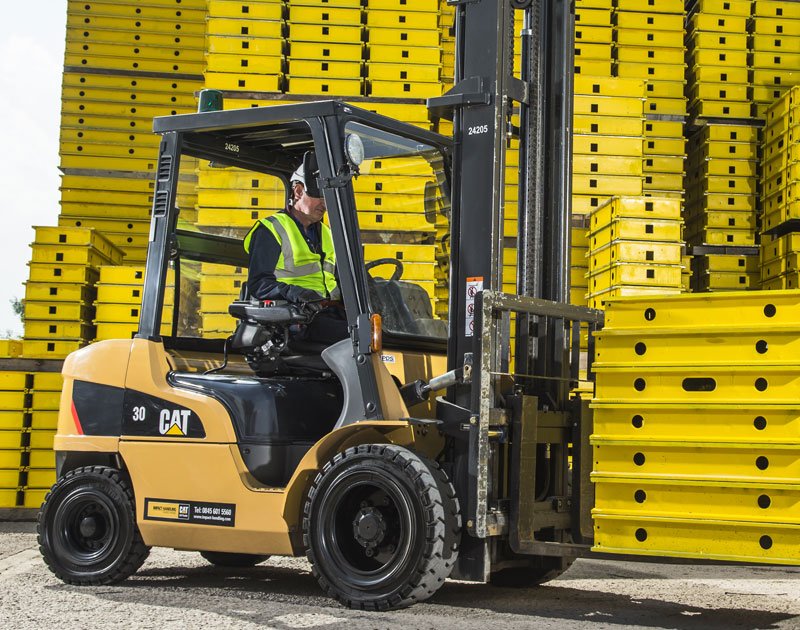
The True Cost of Forklift Downtime
The downtime cost of a forklift extends far beyond just repairing the equipment. When a forklift is out of service, businesses face maintenance labor fees, along with the delivered cost of replacement parts and expedited shipping. These add to the overall true cost of downtime, which includes lost productivity and delayed shipments.
Over time, frequent breakdowns drive up the total ownership cost of the forklift, making it more expensive to operate than anticipated. To avoid escalating costs, it’s crucial to address not only immediate repair needs but also the long-term financial implications of frequent downtime.
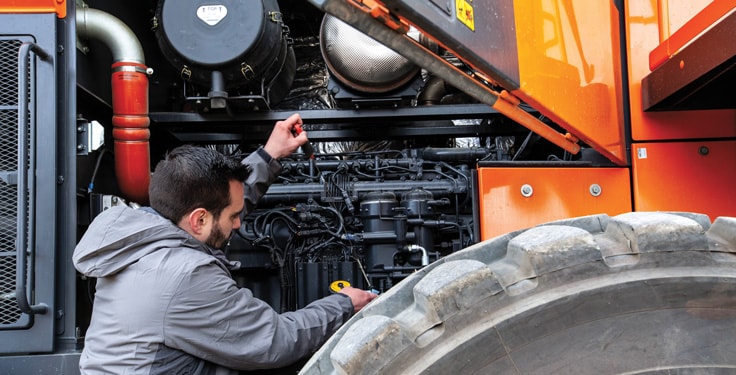
Major Causes of Forklift Downtime
Forklift downtime can often be traced back to preventable factors such as regular wear and tear, human error, and improper handling of heavy loads. Over time, forklifts naturally degrade due to wear and tear, but mishandling by operators can lead to faster breakdowns. Human error, like improper operation or ignoring safety protocols, often results in unexpected downtime.
Additionally, driving on uneven surfaces or consistently operating the forklift under excessive strain can lead to accelerated wear, causing damage to key components. By addressing these factors, businesses can significantly reduce downtime and improve forklift longevity.
Minimizing Forklift Downtime with Planned Maintenance Programs
A well-structured planned maintenance program is essential for reducing forklift downtime. Regular maintenance ensures that minor issues are addressed before they become major problems, thus extending the lifespan of your forklifts and avoiding costly repairs.
By following a detailed maintenance manual, businesses can perform routine checks and repairs at recommended intervals, ensuring that equipment runs smoothly. This proactive approach helps detect potential issues, such as worn parts or fluid leaks, which can lead to unexpected breakdowns if left unattended.
Adhering to forklift specifications is also crucial for optimal performance. Each forklift is designed to operate under specific conditions, and exceeding these limits—whether in load capacity or operating hours—can lead to premature wear. Effective maintenance programs incorporate these specifications, ensuring proper care of all components.
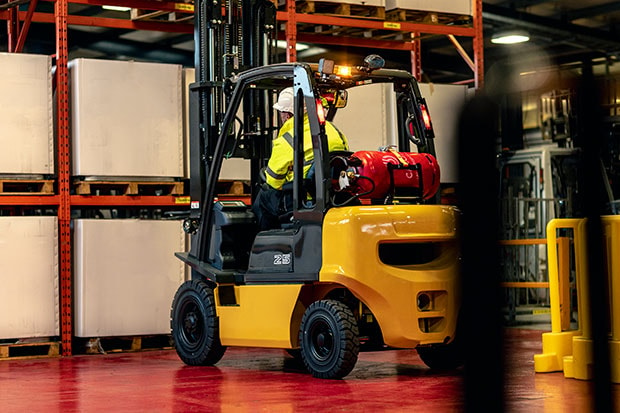
By following the manufacturer’s guidelines and keeping equipment in top condition, businesses can significantly reduce unplanned downtime, improve productivity, and keep repair costs low.
Operator Training: The Key to Reducing Downtime
Proper operator training is vital in minimizing forklift downtime caused by mishandling. Well-trained operators understand the importance of adhering to safety protocols and best practices, which can help avoid accidents and costly breakdowns. Regular refresher training ensures that even experienced operators stay updated on the latest operational techniques and safety standards, reducing the risk of human error.
Employing certified technicians for periodic inspections further prevents unexpected downtime by identifying potential issues before they escalate. Additionally, a robust company policy that enforces safety measures and equipment handling standards keeps operators accountable, ensuring that forklifts are used responsibly and efficiently. Investing in operator training ultimately leads to fewer accidents, less equipment damage, and reduced repair costs.
The Role of Proper Usage and Forklift Capacity
Ensuring proper forklift usage is critical to minimizing wear and tear, reducing breakdowns, and extending the forklift’s operational life. Every forklift has a maximum capacity for loads it can safely handle. Exceeding this limit can strain the forklift’s components, leading to breakdowns and costly repairs. Overloading the lift truck frequently can accelerate component failure, causing prolonged downtime.
Additionally, adhering to recommended operating hours and monitoring engine hours are key to preventing premature wear on the forklift’s engine and hydraulic systems. Excessive engine hours can lead to overheating and more frequent repairs, resulting in increased maintenance costs. By respecting the forklift’s limits and following operational guidelines, businesses can maximize the uptime of their equipment, ensuring it runs reliably and efficiently over the long term.
How Spare Parts and Quality Repairs Can Save Money
Using quality parts and timely replacement parts plays a significant role in reducing downtime and saving money in the long run. Poor-quality or mismatched parts can lead to frequent breakdowns, higher repair costs, and potential safety hazards.
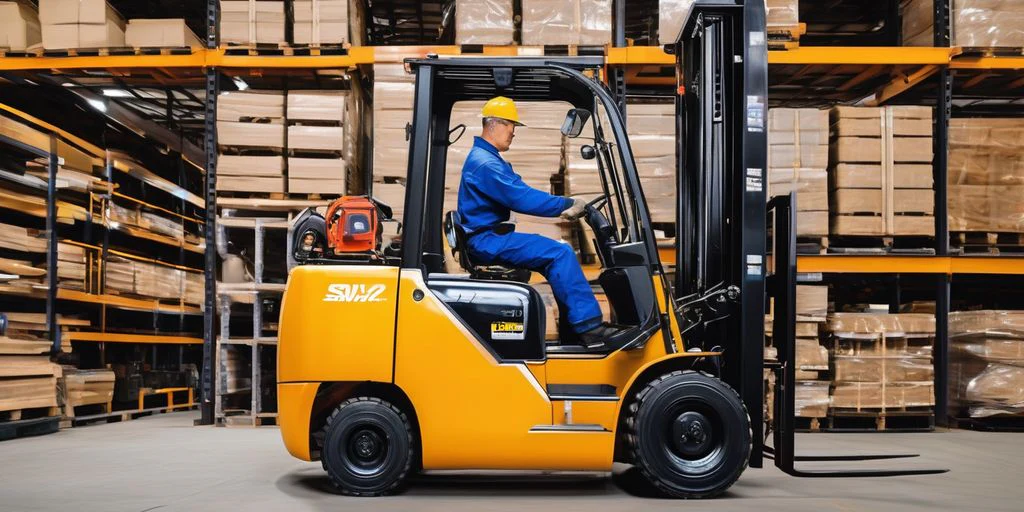
For instance, components like the seat assembly may seem minor, but if poorly maintained or replaced with subpar parts, they can affect operator safety and the forklift’s overall performance. Opting for quality parts ensures that your forklift runs efficiently, reducing the frequency of repairs and prolonging the equipment’s lifespan.
Moreover, working with reliable suppliers allows businesses to anticipate needs for parts and avoid expedited shipping fees for last-minute orders, which can be costly. By planning ahead and keeping essential replacement parts in stock, businesses can address repair issues promptly without incurring additional costs, ensuring smoother operations and fewer delays.
Track Forklift Data to Avoid Downtime
Diligent record keeping is essential for maintaining your forklift fleet and avoiding unnecessary downtime. Keeping a detailed truck’s file that tracks each forklift’s serial number, maintenance history, and repair trends helps monitor the health of your equipment.
Implementing comprehensive maintenance programs based on this data allows for timely repairs and consistent upkeep, ensuring forklifts are always in optimal condition and minimizing unexpected breakdowns.
Why Choose Upright Forklift Repair in Houston & Humble, TX
At Upright Forklift Repair, we understand how critical it is to minimize downtime for your business. Located in both Houston and Humble, TX, our team of certified technicians specializes in comprehensive forklift repair services designed to keep your operations running smoothly. We offer expert maintenance programs tailored to help reduce downtime, avoid accidents, and save money on costly repairs.
Whether you need routine maintenance or emergency repairs, our experienced team is equipped to handle it all, ensuring your forklifts operate safely and efficiently. Contact Upright Forklift Repair today for reliable service and solutions that keep your equipment—and your business—up and running.