In the competitive business environment of Houston and Humble, TX, reducing forklift operational costs is crucial for maintaining profitability and efficiency. Forklifts are indispensable in material handling operations, but without proper management, their maintenance costs can quickly escalate, impacting your bottom line. Local businesses specializing in forklift repair, service, and spare parts must focus on optimizing their operations to stay ahead.
Understanding how to reduce forklift operational costs is vital not only to minimize expenses but also to extend the life of your equipment. By implementing strategic maintenance practices and partnering with a trusted local dealer, businesses can significantly lower forklift maintenance costs.
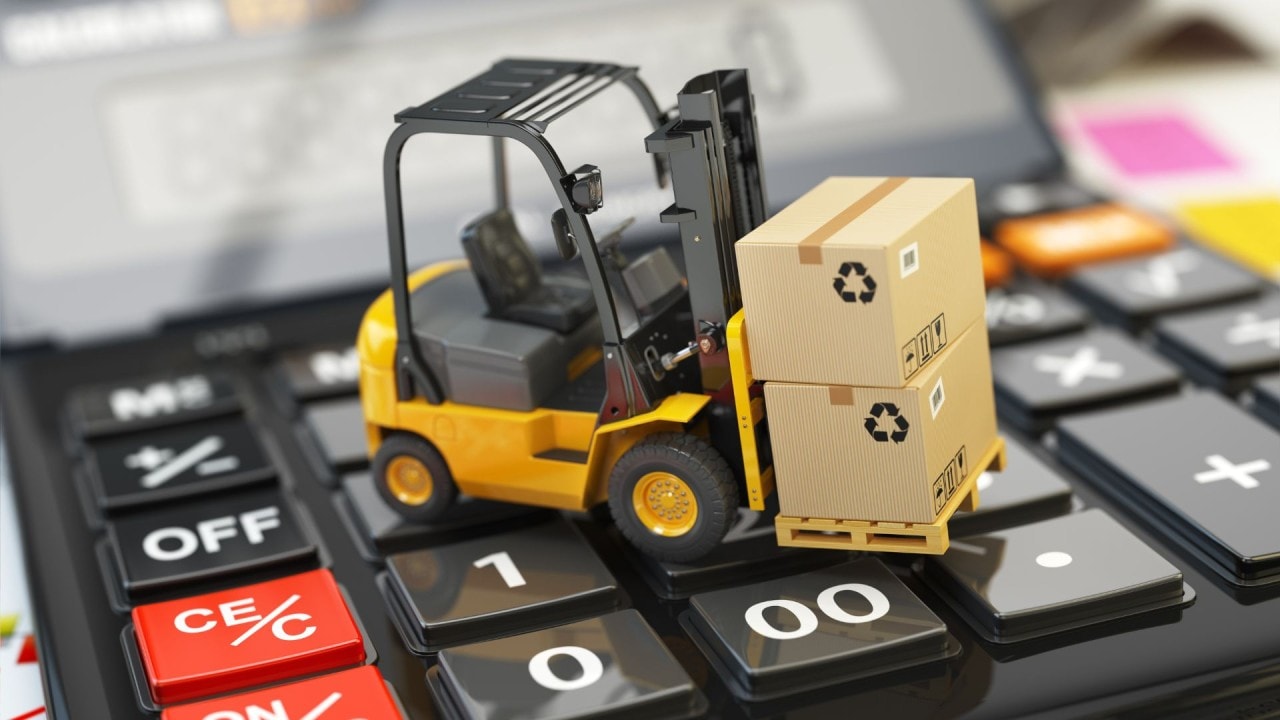
This proactive approach not only prevents costly repairs but also ensures that your forklift fleet remains in optimal condition, maximizing productivity and reducing downtime. Whether you operate a single forklift or a mixed fleet, taking steps to manage maintenance effectively is key to long-term success.
Optimize Forklift Maintenance to Reduce Costs
Effective forklift maintenance is the foundation of reducing operational costs and preventing costly repairs. Regular forklift maintenance is essential for keeping your equipment running smoothly and avoiding unexpected breakdowns that can disrupt your operations. By consistently performing necessary maintenance tasks, you can extend the life of your forklifts and reduce overall maintenance costs.
Regular Forklift Maintenance is Key
A well-structured maintenance program starts with regular forklift maintenance. This involves daily inspections to check for wear and tear, ensuring that all components are in good working order. Creating a checklist of maintenance tasks is crucial; it helps operators focus on key areas such as checking fluid levels, inspecting tires, and testing brakes. Addressing these small issues early can prevent them from turning into costly repairs that require significant downtime.
Preventative Maintenance Measures
Incorporating preventative maintenance measures is another effective way to reduce forklift maintenance costs. By scheduling routine checks and addressing potential issues before they become major problems, you can prevent breakdowns and extend the life of your forklifts. Regularly inspecting and replacing worn parts, such as air filters and belts, helps reduce maintenance costs and keeps your equipment running efficiently. Preventative maintenance not only saves money in the long run but also ensures your forklifts are always ready to perform at their best.
Improve Operator Efficiency and Safety
Enhancing the skills and awareness of your forklift operators is essential to maintaining a safe and efficient workplace. Properly trained operators are more adept at performing routine inspections and basic regular maintenance, which helps to identify and address minor issues before they escalate.
This proactive approach not only ensures the safety of your employees but also helps to reduce forklift operational costs by minimizing the likelihood of accidents and breakdowns.
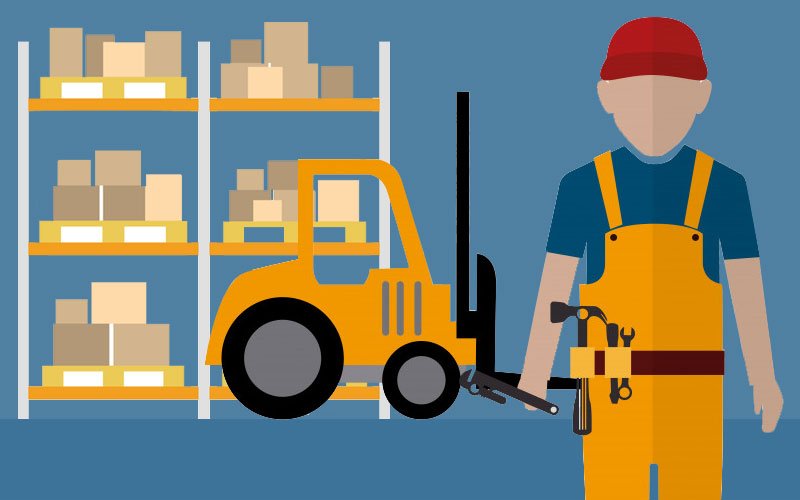
Training Forklift Operators for Success
Investing in proper training for your forklift operators is a smart way to boost both safety and productivity. Well-trained operators are more likely to handle equipment with care, perform accurate routine inspections, and follow best practices that extend the lifespan of your forklifts. This reduces the need for frequent repairs and contributes to a safer working environment, ultimately leading to lower operational costs and fewer disruptions.
Enhance Warehouse Efficiency and Productivity
Optimizing your warehouse layout is a key strategy to improve overall efficiency and reduce operational costs. By strategically organizing storage areas and minimizing unnecessary travel paths, you can significantly reduce the time forklift operators spend moving between tasks. This not only improves productivity but also reduces wear and tear on your equipment, leading to lower forklift maintenance costs in the long run.
Maintaining good floor conditions is another critical factor in enhancing warehouse productivity. Poorly maintained floors can cause excessive wear on forklift tires, leading to frequent replacements and potential downtime. By ensuring that your warehouse floors are smooth, clean, and free of debris, you can minimize the impact on your forklifts, extending the life of their tires and reducing the need for constant maintenance.
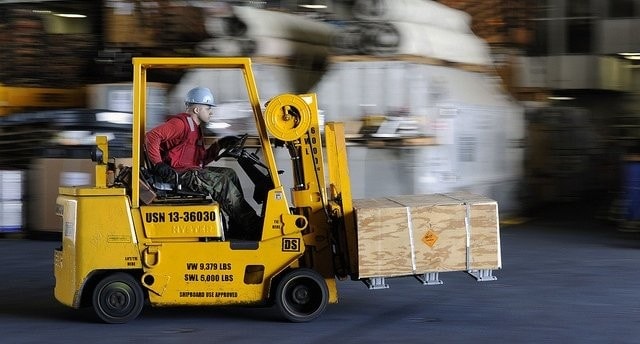
Overall, a well-organized warehouse with good floor conditions supports a more efficient operation, helping to keep your forklift maintenance costs under control and boosting the productivity of your entire material handling process.
Enhance Warehouse Efficiency and Productivity
Improving your warehouse layout and maintaining your equipment properly are crucial steps in boosting overall productivity and reducing operational costs. A well-organized warehouse can significantly streamline operations, reduce travel time for forklift operators, and minimize unnecessary wear on your equipment, leading to lower forklift maintenance costs and improved workflow.
Optimize Warehouse Layout and Design
A strategic approach to optimize warehouse layout can drastically reduce TCO (Total Cost of Ownership) for your material handling operations. By minimizing travel distances and improving access to high-frequency areas, you can enhance productivity and reduce the strain on your fleet.
Additionally, integrating fleet management services allows you to monitor and adjust your layout to align with operational needs, ensuring that your forklifts are used efficiently and maintenance costs are kept to a minimum.
Keep Your Floors in Good Shape
Maintaining good floor conditions is essential to prolong the life of your forklift’s tires and reduce overall wear and tear on your equipment. Floors that are smooth, clean, and free of obstacles help to prevent tire damage and reduce the need for frequent replacements. By keeping your floors in top condition, you not only extend the life of your forklifts but also maintain a safer and more efficient working environment.
Reduce Energy and Material Costs
Selecting the appropriate engine type for your forklifts is a critical decision that can have a lasting impact on your operational expenses. As the industry shifts towards more sustainable practices, considering the benefits of electric forklifts over traditional diesel models can lead to significant savings. Electric forklifts are not only more environmentally friendly, but they also help to reduce fuel consumption and lower your overall energy costs.
Choosing the Right Engine for Your Forklift Fleet
When evaluating your forklift fleet, it’s essential to consider how the fuel consumption of different engine types affects your bottom line. With the upcoming 2040 diesel engine ban, transitioning to electric forklifts can position your business ahead of regulatory changes while also providing long-term cost savings.
Electric models typically offer lower operating costs, reduced maintenance, and a smaller environmental footprint, making them an excellent choice for forward-thinking businesses looking to optimize their material handling operations.
Implement Cost-Saving Strategies
To reduce maintenance costs effectively, businesses should consider implementing simple yet impactful strategies. One such strategy is performing small repairs in-house. By training your team to handle minor fixes, like replacing bulbs or tightening loose components, you can save money on service calls and prevent further damage that might occur if these issues were left unattended. This approach not only cuts down on expenses but also keeps your forklifts in better working condition.
Performing Small Repairs In-House
Taking charge of small repairs within your organization is a smart way to save money. Handling minor fixes like light replacements or adjusting seat belts can prevent small issues from escalating into costly problems. Regularly addressing these smaller tasks helps avoid further damage and ensures that your equipment remains operational without the need for frequent external service calls.
Monitor and Adjust Your Maintenance Programs
Regularly reviewing and updating your maintenance programs is crucial for maintaining cost efficiency. By analyzing the performance of your fleet and adjusting your maintenance schedule as needed, you can optimize operations and keep overall costs low. Effective fleet management involves continuously monitoring the condition of your equipment to ensure that maintenance activities are both timely and cost-effective.
Consider Upgrading Your Fleet Management
Investing in a robust fleet management system can provide significant long-term benefits for your business. Advanced fleet management services allow for real-time tracking of your equipment, helping you monitor usage patterns, schedule maintenance, and reduce unexpected breakdowns. By leveraging technology, you can lower maintenance costs and improve the efficiency of your operations.
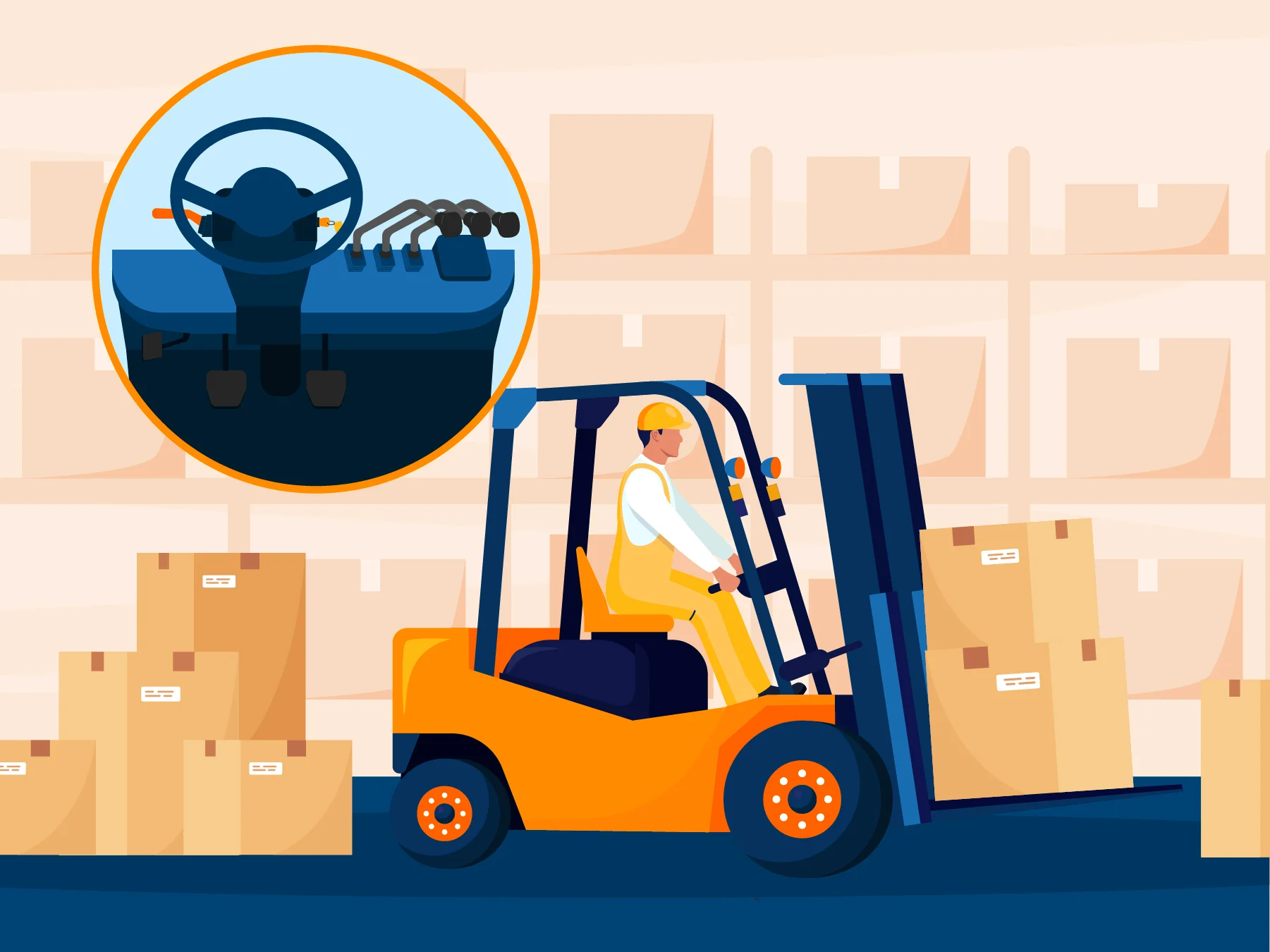
Integrating Technology for Better Fleet Management
Incorporating technology into your fleet management services can be a highly cost-effective strategy. Tools like telematics and data analytics provide valuable insights into your forklift operations, enabling you to schedule maintenance more effectively and avoid unnecessary expenses.
By tracking key performance indicators, you can reduce maintenance costs and extend the lifespan of your equipment, ensuring that your maintenance plan is optimized for both productivity and cost savings.
Partner with a Local Dealer for Support
Partnering with a local dealer for your forklift maintenance, repairs, and parts ensures you have access to timely and cost-effective solutions. Local dealers, like Upright Forklift Repair, offer personalized service, including breakdown service and maintenance tailored to your specific needs.
They also help you maintain inventory by providing quick access to replacement parts, reducing downtime, and keeping your operations running smoothly. Working with a local dealer ensures that your forklifts are always in top condition, which contributes to lower long-term maintenance costs.
Final Thoughts
Reducing forklift operational costs is essential for maintaining a lean, efficient warehouse. Implementing strategies like choosing the right maintenance plan, managing a mixed fleet, and partnering with a local dealer can significantly save money and enhance productivity.
For businesses in Houston and Humble, TX, Upright Forklift Repair offers cost-effective solutions tailored to your specific needs, helping you keep your forklifts in optimal condition and your operations running smoothly. Contact us today to learn how we can help you reduce operational costs and improve your forklift fleet’s performance.