Forklifts, often considered the workhorses of the industrial world, play a pivotal role in ensuring that operations run smoothly in warehouses, construction sites, and many other sectors. These powerful machines, responsible for lifting and transporting heavy loads, are integral to the efficiency and productivity of countless businesses. However, like all machinery, forklifts are not immune to wear and tear. The significance of regular maintenance and repair becomes paramount not only to prolong the machine’s life but to ensure the safety of operators and other workers on the premises. In this comprehensive guide, we will delve into the intricacies of forklift repair, offering insights into common issues, troubleshooting techniques, and preventive measures to keep your forklift running optimally. Whether you’re a seasoned forklift operator or a novice looking to understand the machinery better, this guide is tailored to provide clarity and knowledge on the subject.
Understanding the Basic Components of a Forklift
The forklift, while often seen as a singular piece of machinery, is actually a complex amalgamation of several vital components that work seamlessly together to the lift truck perform its primary function: lifting and transporting heavy loads. Before diving into repair procedures, it’s crucial to familiarize oneself with the key parts of a lift trucks or forklift and their respective roles. This foundational knowledge will not only aid in troubleshooting but also in ensuring optimal operational efficiency.

Mast: Material handling equipment
- The mast is the vertical assembly at the front of the forklift responsible for raising, lowering, and tilting the load. It consists of interlocking rails that provide support and guidance for the forks as they move upwards or downwards.
Tires:
- Depending on the working environment, forklifts may be equipped with either pneumatic (air-filled) or cushion (solid rubber) tires. These tires are specially designed to bear heavy loads and provide stability to the machine during operations.
Counterweight:
- Located at the rear of the forklift, the counterweight is crucial for balancing the machine. It counteracts the weight of the load being lifted, preventing the forklift from tipping forward.
Forks:
- As the name suggests, the forks are the pronged extensions that slide into pallets or beneath loads to lift and transport them. They are adjustable to fit various load sizes.
Overhead Guard:
- This is a protective frame situated above the operator’s seat. Its primary purpose is to shield the operator from falling objects or debris, ensuring their safety during forklift operations.
Tilt Cylinders:
- These hydraulic cylinders allow the mast and the forks to tilt forwards or backwards. This tilting mechanism helps the operator to position the load at the desired angle, facilitating safer and more efficient loading or unloading processes.
Each of these components, while serving a specific purpose, is integral to the forklift’s overall operation. Regular monitoring and maintenance of these parts ensure that the machine functions correctly and safely. As we delve deeper into forklift repair in subsequent sections, this foundational understanding of forklift parts will prove invaluable.

Common Forklift Problems and their Symptoms
A forklift, like any machine, may occasionally experience issues that hinder its performance. Recognizing these problems early on can help prevent potential damage to lift equipment, ensure the safety of the operator, and avoid costly downtimes complex repairs. Below, we explore some of the most common forklift problems and their tell-tale symptoms:
- Difficult Steering:
- Symptoms: The forklift becomes harder to steer or might even resist turning in a particular direction.
- Possible Causes: Low hydraulic fluid levels, worn-out steering components, or issues with the steering cylinder.
- Unresponsive Lifting or Lowering:
- Symptoms: The forks do not move up or down, despite commands, or they might do so at an unusually slow rate.
- Possible Causes: Depleted hydraulic fluid, malfunctioning lift pump, or issues with the mast’s chains and rollers.
- Overheating:
- Symptoms: The forklift’s temperature rises beyond the standard operating range, often accompanied by the release of steam or smoke. An overheated engine might also cause the forklift to shut down unexpectedly.
- Possible Causes: Blocked or dirty radiator, low coolant levels, faulty water pump, or excessive load weight causing strain on the engine.
- Brake Issues:
- Symptoms: The forklift does not stop promptly when brakes are applied, or there might be a squealing sound during braking. The pedal might also feel unusually soft or hard.
- Possible Causes: Worn-out brake pads or shoes, low brake fluid levels, or air trapped in the brake lines.
- Unusual Noises:
- Symptoms: Strange sounds, such as grinding, squealing, or knocking, emanate from the forklift during operation.
- Possible Causes: These noises can have various origins, from loose parts, lack of lubrication, issues with the transmission, or even engine malfunctions.
Awareness of these common problems and their associated symptoms can greatly assist operators highly skilled certified technicians and maintenance personnel who service vehicles in quickly diagnosing issues. Swift action can then be taken to rectify the problem, ensuring the forklift’s longevity and the safety of its environment. In the following sections, we will delve into troubleshooting and repair solutions for these challenges.

Pre-Repair Safety Measures
Before embarking on any forklift equipment repair procedure, it’s paramount to prioritize safety. Forklifts, by their very nature, are heavy-duty machines capable of causing harm if not approached with caution during repairs. Here, we delve into essential safety measures that should be taken before and during the forklift equipment repair process.
- Importance of Safety First:
- Understanding the Risks: Before initiating any repairs, it’s vital to comprehend the potential risks involved. Mishandling or misunderstanding a forklift’s components could lead not only to further damage to the machine but also personal injury.
- Prioritizing Safety: No matter the urgency of the repair, safety should never be compromised. Taking shortcuts or bypassing safety procedures can lead to severe consequences.
- Ensuring the Machine is Powered Down:
- Shutting Down: Always turn off the forklift and remove the key before starting any repair work. This action prevents accidental startups that could endanger the repair person.
- Disconnecting the Battery: For electric forklifts, disconnecting the battery ensures that there’s no active electrical current, further minimizing the risk of electrical shocks.
- Utilizing Safety Signage to Indicate Ongoing Repairs:
- Visibility of Repair Zone: It’s essential to demarcate the repair area clearly. Using safety cones, barriers, or caution tape can help indicate that repair work is in progress.
- Informative Signage: Using signs that state “Repair in Progress” or “Do Not Operate” alerts other personnel to stay clear of the forklift and not attempt to use it during the repair process.
- Wearing Appropriate Personal Protective Equipment (PPE):
- Protective Eyewear: Safety goggles or glasses shield the eyes from sparks, debris, or any fluids that might splash during the repair.
- Gloves: Durable gloves can protect hands from sharp or hot components and also provide a better grip on tools.
- Steel-toed Boots: These protect feet from any heavy components that might accidentally drop.
- Ear Protection: If working in an environment with loud noises or using noisy tools, earplugs or earmuffs are essential to protect hearing.
In conclusion, the adage “better safe than sorry” rings especially true when dealing with machinery repairs. Following these safety protocols not only ensures the well-being of the repair personnel and industrial equipment, but also guarantees that the forklift is repaired without inflicting further damage to industrial equipment. Remember, a safe working environment is a productive one.
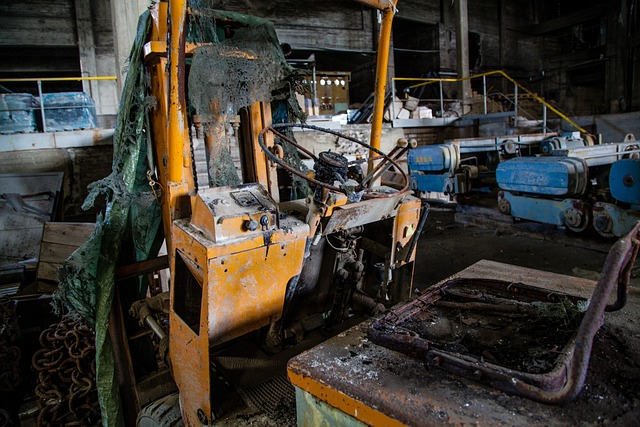
Basic Troubleshooting Techniques
Before diving into in-depth repair processes or calling in professionals, it’s often prudent to undertake some basic troubleshooting techniques. These initial steps can help identify obvious issues, and in some cases, may even lead to simple solutions. Here’s a guide to fundamental troubleshooting techniques every forklift operator or maintenance personnel should know:
- Conducting a Visual Inspection for Obvious Damages:
- Exterior Assessment: Begin by walking around the forklift, looking for any visible signs of wear, cracks, or damage on its body and tires.
- Mast & Fork Examination: Check the mast’s alignment, and inspect the forks for any deformities or visible signs of wear and tear.
- Hose and Belt Inspection: Look for cracks, fraying, or any disconnections in hoses and belts. These components should be snug and free of damage to function correctly.
- Listening for Unusual Sounds:
- Startup Sounds: When you turn on the forklift, pay close attention to any abnormal noises during startup, such as grinding or hissing sounds.
- Operational Noises: As you operate the forklift, listen for any unusual sounds when lifting, lowering, or maneuvering. Clicking, knocking, or squealing can be indicators of specific issues.
- Identifying Source: Try to pinpoint the location of the noise. Is it coming from the rear, near the engine, from the mast, or perhaps the wheels? Narrowing down the source can significantly aid in the diagnostic process.
- Checking Hydraulic Fluid Levels and Battery Connections:
- Hydraulic Fluid Check: Locate the hydraulic fluid reservoir and check its level. If the fluid is below the recommended level, it might lead to issues like unresponsive lifting or steering difficulties. Also, note the color and consistency of the fluid; it should be clear without any visible contaminants.
- Battery Connections: For electric forklifts, ensure that the battery connections are clean and snug. Corrosion on terminals or loose connections can lead to power issues or sporadic forklift performance.
These basic troubleshooting techniques serve as the first line of defense in identifying and potentially rectifying issues with your forklift. While they might not resolve all problems, they can provide valuable insights into what might be going wrong, guiding subsequent repair steps or informing discussions with professional repair technicians.
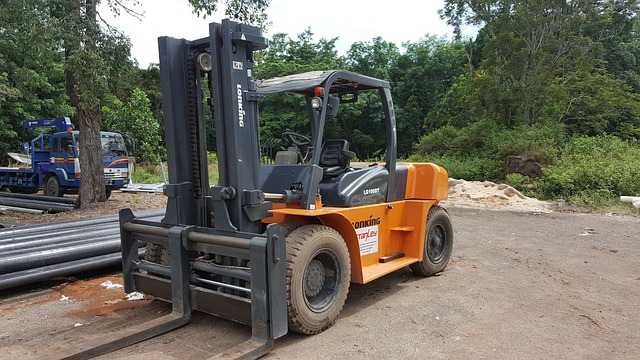
Delving into Common Repair Procedures
Forklift issues, once identified, often require targeted repair procedures to rectify. The following are standard procedures to address some of the most common forklift problems:
1. Steering Issues
- Checking Hydraulic Fluid Levels:
- Ensure the hydraulic fluid reservoir is filled to the recommended level. Low fluid can result in stiff or unresponsive steering.
- Inspecting for Leaks in the Steering Mechanism:
- Examine hoses, seals, and connections for any signs of leaks. If a leak is identified, it might necessitate a seal replacement or hose repair.
- Examining the Condition of the Steering Wheel and Axles:
- Check for wear, damage, or misalignment in these components. Misaligned axles or a damaged steering wheel can impede smooth steering.
2. Lifting and Lowering Concerns
- Checking Fluid Levels in the Lift Cylinders:
- Ensure that the hydraulic fluid in the lift cylinders is at the optimal level for proper lifting and lowering actions.
- Examining Hoses for Leaks:
- Look for any wet or oily spots along the hydraulic hoses, which may indicate a leak.
- Assessing the Condition of the Mast and Forks:
- Check the mast’s rails and the forks for any signs of wear, deformation, or misalignment that might hinder their movement.
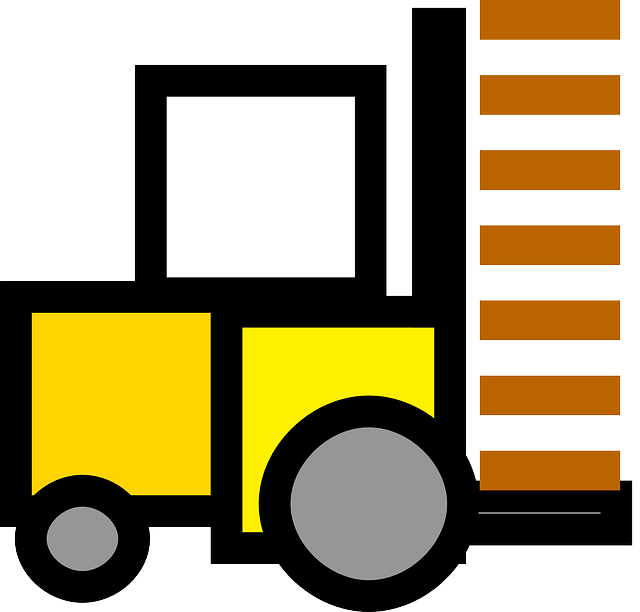
3. Overheating
- Cleaning the Radiator and Ensuring It’s Free of Obstructions:
- Dust, debris, or dirt accumulation on the radiator can impede airflow and lead to overheating. Cleaning it regularly can enhance its efficiency.
- Checking Coolant Levels:
- Ensure that the coolant reservoir is filled to the recommended mark. Low coolant levels can result in the engine overheating.
- Examining the Water Pump for Proper Functionality:
- Check for any leaks or noises from the water pump. A malfunctioning pump can disrupt coolant circulation, causing the engine to overheat.
4. Brake Repairs
- Checking Brake Fluid:
- Inspect the brake fluid reservoir and make sure it’s adequately filled. Low brake fluid can reduce braking efficiency.
- Inspecting Brake Pads and Discs for Wear:
- Examine the brake pads and discs. If they show signs of excessive wear, replacements might be in order.
- Ensuring the Proper Operation of Hand and Foot Brakes:
- Test both hand and foot brakes to ensure they respond as expected. Any lag or unresponsiveness may require further investigation.
5. Addressing Unusual Noises
- Identifying the Source (Engine, Mast, Wheels):
- Pinpointing where the noise originates can narrow down potential causes and solutions.
- Checking for Loose Components:
- Inspect for any components that might have become loose or are vibrating excessively, leading to noise.
- Lubricating Moving Parts as Needed:
- Noise often results from friction. Proper lubrication of moving parts like chains, rollers, and joints can eliminate such noises and ensure smoother operation.
In summary, while these repair procedures tackle common forklift issues, always consult the service forklift’s manual and, when in doubt, seek the expertise of professional technicians. Proper repair ensures the longevity of the machinery and the safety of service vehicles and those operating it.
Forklift Maintenance Tips for Preventing Frequent Repairs
Preventive maintenance is the cornerstone of prolonged forklift lifespan and efficient performance. Often, regular upkeep can avert the necessity for frequent repairs, saving both time and money. Here are some pivotal maintenance tips to keep your forklift in tip-top shape:
1. Regularly Checking and Changing Fluids:
- Hydraulic Fluid: Regularly inspect the hydraulic fluid levels and refill as necessary. Over time, contaminants can accumulate in the fluid, so it’s essential to change it at intervals recommended by the manufacturer.
- Coolant: Ensure that the coolant is always at the recommended level. Replace old coolant with fresh coolant periodically to maintain optimal engine temperatures.
- Oil: Changing engine oil at stipulated intervals ensures the engine runs smoothly, reducing the chances of overheating or wear.
2. Keeping the Machine Clean from Debris and Dust:
- Exterior Cleaning: Regularly wash the exterior of the forklift to remove dust, grime, and any corrosive substances. This not only keeps the machine looking good but also ensures better visibility and functionality.
- Radiator: Periodically cleaning the radiator ensures efficient cooling. Dust and debris can clog it, leading to overheating issues.
- Air Filters: Change or clean air filters routinely. A clogged filter can restrict airflow, causing the engine to work harder and reducing fuel efficiency.
3. Proper Battery Maintenance:
- Regular Inspections: For electric forklifts, inspect the battery for any visible damages, leaks, or corroded terminals.
- Clean Terminals: Keeping battery terminals clean and tight ensures efficient power transfer and reduces the chances of electrical issues.
- Charge Cycles: Follow recommended charge cycles. Overcharging or undercharging can reduce battery life and performance.
4. Routine Inspections of Tires, Brakes, and Other Key Components:
- Tires: Check tires for wear, cuts, or punctures. Replace them when they show signs of excessive wear or damage. Properly inflated tires ensure better load handling and fuel efficiency.
- Brakes: Inspect brake pads, discs, and fluid levels. Addressing any brake issues promptly ensures the safety of the operator and the load.
- Mast and Forks: Regularly inspect the mast’s rails and the forks for signs of wear or deformation. Lubricate the necessary parts to ensure smooth movement.
In conclusion, the adage “An ounce of prevention is worth a pound of cure” couldn’t be more accurate for forklift maintenance. Adopting these preventive measures can greatly reduce the frequency of repairs, ensuring that your forklift operates efficiently and safely for years to come.
When to Call in a Professional For Lift Trucks
While many forklift issues can be addressed through basic troubleshooting and maintenance techniques, there are situations when professional intervention is not only recommended but also imperative. Understanding the distinction between a DIY-fixable problem and one that requires expert hands is crucial for both the safety of the operator and the longevity of the machinery. Here’s a guide on when to call in a professional:
1. Limitations of DIY Repairs:
- Knowledge Gaps: Even the most diligent forklift operators may not possess the in-depth knowledge required to address complex mechanical or electrical issues.
- Tool Limitations: Some repairs might necessitate specialized tools, which are typically not found in standard toolkits.
- Warranty Concerns: Undertaking DIY repairs might void the manufacturer’s warranty, leading to potential challenges if major issues arise later.
2. Recognizing When the Problem is Beyond Basic Troubleshooting:
- Recurrent Issues: If a problem persists or reoccurs shortly after a DIY fix, it might indicate a deeper, underlying issue.
- Complex Error Codes: Modern forklifts come equipped with diagnostic systems that display error codes. While some might be straightforward, others can be intricate and require a professional’s interpretation.
- Significant System Failures: Issues like complete hydraulic system failures, total brake malfunctions, or widespread electrical problems should be left to professionals.
3. The Significance of Trained Professionals in Ensuring Safety and Proper Repairs:
- Expertise: A trained technician has the knowledge and experience to pinpoint and address issues efficiently, ensuring that the repair is both effective and lasting.
- Safety Assurance: Professionals are trained to handle repairs safely, mitigating the risks of injury or further damage to the forklift.
- Proper Calibration: Post-repair, professionals can calibrate systems, ensuring that the forklift operates at optimal efficiency and safety.
In conclusion, while taking the initiative to address minor or forklift service issues can be commendable, recognizing one’s limits is paramount. When in doubt, it’s always safer and often more cost-effective in the long run to enlist the expertise of a trained professional. Their skills and experience ensure that your machinery is repaired correctly, safely, and your replacement equipment is set to serve you reliably for the foreseeable future.
Final Thoughts on Maintaining Safe, Efficient Forklift Performance
The intricate dance between machinery and its operator is a bond that relies heavily on trust. For a serious forklift service department, which plays a pivotal role material handling equipment used in many industries, this trust is built on the foundation of consistent performance and reliability. This article has journeyed through the multifaceted world of forklift repair and maintenance, but if there are two takeaways that stand out, they are:
- The Importance of Proactive Maintenance: As with most things, prevention is often better than the cure. Regular maintenance not only extends the lifespan of the forklift but also ensures it operates at peak efficiency. By addressing minor issues before they escalate, businesses can save significant time and money in the long run.
- Safety Above All: Forklifts, while invaluable, are also powerful machines with the potential for harm if not treated with respect. Whether it’s during regular operation, basic troubleshooting, or more extensive repairs, safety should always be the paramount concern. By following best practices and knowing when to call in professionals, operators can ensure not just their safety but also that of their colleagues and the machinery itself.
X. References and Additional Resources
While this guide provides a comprehensive overview, forklift maintenance and repair is a vast field with continuous advancements and nuances specific to various models and brands. For further exploration of various job related topics, here’s a list of resources:
- Forklift Operator Manuals: Always the first point of reference, these manuals are tailored to specific forklift models and offer valuable insights into maintenance schedules, troubleshooting tips, and safety guidelines.
- Forklift Academy: An online platform offering training modules, safety guidelines, and repair tutorials for various forklift models.
- ForkliftSafety.com: A comprehensive resource dedicated to forklift safety, offering training materials, safety products, and in-depth articles on maintenance and repair.
- Local Dealerships and Service Centers: These centers often offer workshops, training sessions, and have professionals on hand to address queries related to specific forklift brands and models.
- Industry Forums: Platforms likeForkliftaction or other industry-specific forums can be valuable for discussions, sharing experiences, and seeking advice on unique issues or challenges.
In the journey of understanding, maintaining, and repairing forklifts, continuous learning and an emphasis on safety are key. By arming oneself with knowledge and resources, operators can ensure their machinery remains an asset, not a liability. Safe lifting!
We service the greater Houston area and Humble texas areas, and all areas surrounding Houston TX.
We have over 20 years of combined experience to services your exact needs.